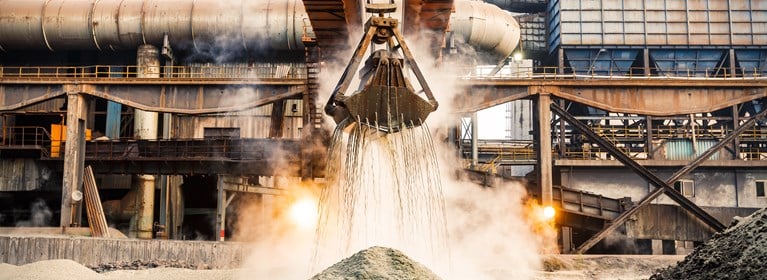
Metallindustrie | Herstellung | Kransysteme | Antriebstechnik | by | 23 Sep 2020
PRODUKTE UND DIENSTLEISTUNGEN:
- IMPULSE®•G+/VG+ Serie 4 Frequenzumrichter
- IMPULSE®•Link Software mit drahtlosem Zugriff
- Erweiterte Schaufelsteuerung Kundenspezifische Software
- Dynamische Bremswiderstände
- Speicherprogrammierbare Steuerung (SPS)
- Mensch-Maschine-Schnittstelle (HMI)
- Dienstleistungen der Division Automation
Herausforderung
- Entwicklung einer automatisierten Lösung, um manuell betätigte Steuerungen zu ersetzen
- Ermöglichen Sie einen konsistenten Reinigungsplan für den Zundergrubenklärer
- Reduzieren Sie die Abhängigkeit von manuellen Kontrollen
- Bereitstellung eines effektiveren Prozesses zum Filtrieren von Walzzunder aus Wasser
Lösung
- Installierte vollautomatische Lösung, die die Beteiligung von Menschen in Gefahrenbereichen begrenzt
- Ermöglicht eine konsistente, genaue Bewegung für eine effiziente Reinigung der Waagengrube
- Integrierte drahtlose Kommunikation für kontinuierliche Systemanalyse und -diagnose
- Verbesserte Sicherheit, Betriebszeit und Produktivität mit kranspezifischer Spezialsoftware
Ein Stahlwerk stellte fest, dass sein Walzwaagen-Klärbecken ineffizient war, was gelegentlich zu Anlagenschäden und Unterbrechungen des Produktionsprozesses führte. Walzzunder ist ein Nebenprodukt von Wasserstrahlen zur Kühlung von Stahl. Ein Klärbeckenkransystem trennt den Walzzunder vom Wasser, sammelt ihn in Haufen und entnimmt das Produkt für den Wiederverkauf. Dann wird das restliche Wasser aufbereitet und für die Prozesse im Stahlwerk umgeleitet. Das System musste aufgerüstet werden, um einen reibungslosen Ablauf zu gewährleisten.
ALLE IMPULSE-FREQUENZUMRICHTER® DURCHSUCHEN
Das ursprüngliche Kransystem verwendete veraltete Schützsteuerungen und wurde von Technikern manuell bedient, was sie von ihren Hauptaufgaben abhielt. Aufgrund fehlender Anlagenüberwachung liefen die aufgestauten Zunderhaufen im Außenbereich über und störten die Kranbewegung. Ablagerungen durch Kalkablagerungen im recycelten Wasser verstopften auch die Sprühdüsen im Stahlwerk und verursachten kostspielige und zeitaufwändige Wartungen.
Das Automatisierungsteam war in der Lage, eine innovative automatisierte Lösung zu entwickeln, um die Sicherheit, Betriebszeit und Produktivität des Stahlwerks zu verbessern. Das neue System umfasste komplette Schalttafeln, die Frequenzumrichter IMPULSE®G+ und VG+ der Magnetek-Marke mit® kundenspezifischer, kranspezifischer Software, dynamischen Bremswiderständen und einer integrierten speicherprogrammierbaren Steuerung (SPS) und einer PC-basierten Mensch-Maschine-Schnittstelle (HMI). Alle waren über Ethernet-Kommunikation miteinander verbunden, um Analyse- und Diagnoseinformationen zu melden.
Das neue Schachtklärsystem ist so programmiert, dass es automatische Zyklen zu bestimmten Zeiten einleitet, und wurde entwickelt, um Sicherheitsüberprüfungen durchzuführen und sicherzustellen, dass alle Parameter erfüllt sind, bevor der Betrieb beginnt. Wenn ein Parameter nicht erfüllt wird, kann ein Techniker auf das HMI zugreifen, das Informationen aus dem System anzeigt, um festzustellen, welcher Parameter den Betrieb verhindert. Das HMI sowie zusätzliche Computer und Überwachungsgeräte befinden sich in einem Off-Kran-Kontrollraum, der den Technikern eine Zentrale bietet und bei Bedarf einen Fernzugriff ermöglicht. Die IMPULSE®•Link-Software, die eine einfache Programmierung, Überwachung und Fehlerbehebung für mehrere Frequenzumrichter ermöglicht, trägt dazu bei, dass der Kran betriebsbereit bleibt, indem Analyse- und Diagnoseinformationen auf dem HMI im Kontrollraum angezeigt werden.
Sobald die Sicherheitsüberprüfungen abgeschlossen sind, verlässt der Klärkran seine Parkposition und fährt zum dafür vorgesehenen Behälter im Walzzenblech. Um die Reinigungssequenz zu bestimmen, misst der Hub-Encoder die Höhe der Schuppenstapel an jedem Pick-Punkt und kehrt zum höchsten Punkt zurück, sobald alle Pick-Punkte gemessen und aufgezeichnet wurden, wobei alle Punkte, die bereits unter dem Sollwert der Reinigungstiefe liegen, weggelassen werden. Das Hebezeug, das von IMPULSE•VG+ Serie 4 Antrieben der Marke Magnetek gesteuert wird, senkt eine Schaufel in die Waagengrube, bis ein schlaffer Kabelzustand erkannt wird. Die Hakenhöhenmessung der IMPULSE-Antriebe verwendet ein inkrementelles Encoder-Signal, um die Hakenhöhe aus einer kalibrierten Position zu bestimmen. Die integrierte Bucket Control Software in jedem Antrieb steuert die verschiedenen Schaufelbewegungen und bietet dem Bediener den Öffnungs-/Schließstatus der Schaufel, auch unter Wasser.
Die Wagen- und Brückenbewegungen, die von Magnetek-Antrieben der Marke IMPULSE•G+ Serie 4 gesteuert werden, verwenden Absolutwertgeber für die Positionierung, die es einfach machen, die Waage zum Aufnehmen und Entfernen zum Kippbereich zu bewegen. Das computergesteuerte System überwacht die Zunderablagerungen im Deponiebereich, so dass der Kran automatisch einen Deponieplatz auswählen und jedes Mal einen anderen Standort auswählen kann, um die Menge an Zunder an jedem Standort zu minimieren. Die Pfähle werden in gleichmäßigeren und handlicheren Größen gesammelt, was dazu beiträgt, Hindernisse für den Kran zu minimieren und eine einfache Entsorgung zu gewährleisten.
Durch die Integration in die IMPULSE-Antriebe erfordert die Ethernet-Kommunikation weniger Verkabelung im System, ermöglicht den Fernzugriff zur Anpassung von Parametern und vereinfacht die Programmierung der SPS. Um die Inbetriebnahme zu unterstützen, griffen die Techniker vom Magnetek-Werk in Menomonee Falls, Wisconsin, aus auf das drahtlose System zu, um die Software genau an die Betriebsanforderungen anzupassen.
Heute arbeitet das vollautomatische Klärsystem des Kunden ohne menschliches Eingreifen. Das recycelte Wasser, das in pflanzlichen Prozessen verwendet wird, ist sauberer und erfordert weniger Aufbereitung. Saubereres Wasser führt auch zu weniger Reparaturen von Anlagen. Darüber hinaus können die Techniker ihre Hauptaufgaben effizienter erledigen und überlassen der Automatisierungstechnik die Steuerung des Klärbeckensystems. Die Verlagerung der Überwachungsausrüstung vom Kran hat eine viel sicherere Arbeitsumgebung geschaffen, und mit kontinuierlichen Analysen und Diagnosen können die Bediener besser über den Systemstatus informiert bleiben, was bei der Planung der Gerätewartung hilft. All diese Verbesserungen zusammen haben zu einem sichereren und effizienteren Stahlwerk für den Kunden geführt.
Automatisiertes Scale-Grubenkransystem
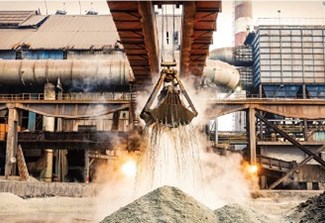