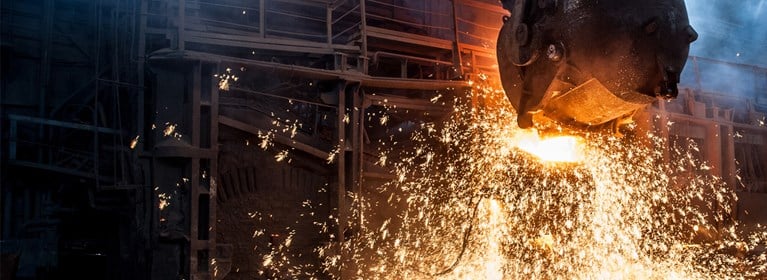
Automatisiertes Einschienenbahnsystem für heiße Metalle
Metallindustrie | Kransysteme | von Magnetek | 01 Sep 2011
Hintergrund
Zwischen einem amerikanischen und einem mexikanischen Unternehmen wurde ein Joint Venture zur Stahlproduktion gegründet. Das neue Walzwerk benötigte eine Möglichkeit, den geschmolzenen Stahl zwischen den Schmelzöfen und den Gießbereichen zu bewegen. Es wurde entschieden, dass die beste Methode dafür die Installation einer Einschienenbahn mit drei Trägern ist. Um den Bediener bei der Positionierung der Ladung zu unterstützen, wurde eine Auto-Dispatch-Funktion hinzugefügt.
Systembeschreibung
Die Hubbewegung wird durch einen Antrieb der IMPULSE® P3 Serie 2 gesteuert, und die Katzbewegung auf dem Träger wird durch den V7 Yaskawa-Antrieb gesteuert. Der Träger betätigt den Kippmechanismus für die Schaufel. Die Positionierung des Hebezeugs erfolgt über einen vierstufigen Getriebeendschalter und die Positionierung der Laufkatze über Näherungssensoren. Eine Allen-Bradley ControlLogix-SPS steuert den Auto-Dispatch-Betrieb. Ein Magnetek-Funksystem ermöglicht es jedem von sechs Sendern, einen der drei Träger nach dem Prinzip "Wer zuerst kommt, mahlt zuerst" zu steuern. Ein Anhänger kann an jeden der Träger angeschlossen werden, um ihn zu steuern, falls ein Funkgerät ausfällt. Optoelektronische Sensoren werden eingesetzt, um zu verhindern, dass Träger ineinander laufen.
STÖBERN SIE IN UNSEREN IMPULSANTRIEBEN®
Betrieb des Systems
Bevor Stahl in die Schaufel gegossen wird, wird die Schaufel im Bereich der Legierungsbehandlung beschichtet. Nach der Behandlung bewegt der Bediener den Träger und die Schaufel mit dem Funksender manuell in den Schmelzbereich. Wenn der Behälter den Schmelzbereich erreicht, senkt der Bediener den Eimer auf das niedrige Niveau ab, damit er sich unter Hindernissen in der Nähe der Öfen bewegen kann. Sobald der Eimer an einer der vier Gießstellen positioniert ist, wird er manuell befüllt und dann manuell aus dem Bereich entfernt. Wenn sich der Betonierort nicht mehr befindet, stellt der Bediener das Funkgerät auf Auto, schaltet den Versand auf den Betonierort #1 oder #2 um und schaltet den Sender aus. Der Sender muss ausgeschaltet werden, damit der nächste Bediener mit seinem Sender die Kontrolle über den Träger übernehmen kann. Das Hebezeug fährt dann in die volle Position und beginnt mit der Fahrt zum ausgewählten Betonierort. Der Träger fährt weiter zum Betonierort und wird in der Kurve langsamer. Wenn der Spediteur den ausgewählten Standort erreicht, stoppt er. Der nächste Bediener schaltet dann seinen Sender ein und stellt ihn in den manuellen Modus, um den geschmolzenen Stahl zu gießen. Nachdem der Bediener mit dem Einschenken fertig ist, schaltet er den Behälter auf Auto, drückt die Versandtaste und schaltet den Sender aus. Das Hebezeug hebt sich dann in die volle Position und fährt in den Bereich der Legierungsbehandlung. Während der Fahrt in den Kurven und bei der Annäherung an den Behandlungsbereich der Legierung läuft der Träger mit langsamer Geschwindigkeit, um ein zusätzliches Maß an Sicherheit für die Bewegung mit geschmolzenem Stahl zu bieten. Wenn der Träger den Behandlungsbereich der Legierung erreicht, stoppt er und der nächste Bediener übernimmt manuell die Kontrolle über den Träger. Der Zyklus wiederholt sich dann.