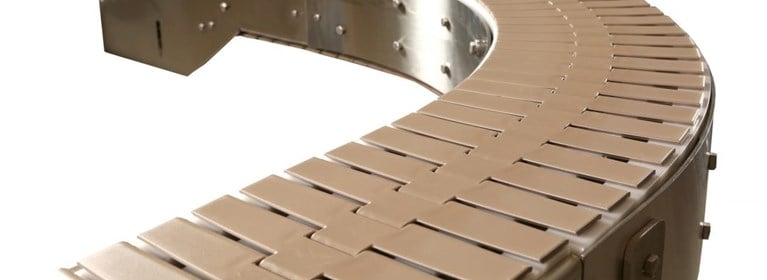
4 Factors to Consider When Choosing a New Conveyor
by Many factors can go into choosing a conveyance system that meets both industry requirements and your company’s unique needs. That’s why we’ve broken down four key aspects to consider when specifying a new conveyor system. | 06 Nov 2022
1. Product and Materials
Product specifications should be the first consideration when looking at any production equipment, especially for conveyance systems. Product size and weight are vital details to ensure the chosen conveyor is ideal for the application.
In the case of large products or high accumulation weights, a smaller conveyor with a lightweight motor will simply not have enough power to move product efficiently. On the flip side, if you’re running small, lightweight products on a conveyor meant for 50lb+ products, the unit is overpowered for the application. A smaller conveyor would work just as well with more energy efficiency.
Additionally, the material a product or packaging is made of should be taken into consideration when selecting the conveyor and accessories to be used. Certain packaging materials and belt combinations may not have enough friction to keep product in place as it moves down the production line, which can result in it slipping around the belt or off the conveyor altogether causing damage and a hazard for operators.
This article by ProSource takes a closer look at how packaging materials can significantly impact the machinery and packaging process a company utilizes.
2. Environment
Understanding the environment a conveyance system is in is vital to ensuring the machinery meets any necessary compliance requirements, and to be sure the equipment is designed to withstand any potential harsh environmental factors.
For example, in a sanitary setting, stainless steel is the only way to go, but some conveyors are designed for wipe-down only cleaning, whereas others can handle high pressure or chemical cleaning procedures on a regular basis. A wipe-down only conveyor may handle a high-pressure wash here or there, but over time it causes significant wear and breakdown of the belt.
3. Integrations
What, if anything, will be integrated with a conveyance system? Does the application utilize robotics or operators to interface with product while it runs through the production process? Do products need to run through a clean room at any point during manufacturing? Or will it simply need sensors to assist with inspection or indexing? All these factors can make a difference in the conveyor design.
Our team of engineers uses these details to create a custom design that fully integrates with the rest of the manufacturing system. Understanding where the conveyor and products will interface with other machinery or employees is vital.
4. Flexibility
Finally, consider the flexibility of any machinery chosen for a production process. In today’s ever-changing economic environment, companies need to be flexible and innovative to stay ahead, which means their manufacturing must also adapt to changes.
A conveyance system capable of running a range of products and materials with quick changeover, as well as one that can be customized for different processes, can make the difference in how well a company can shift its production to meet demand. When any piece of machinery has features that allow it to be adjusted for different product needs, that means a company will not need to purchase an entirely new system to accommodate something new.
Dorner’s Engineered Solutions Group is Here to Help
Our team of knowledgeable engineers and application specialists is here to walk you through the entire process of creating a custom conveyance system. From getting specifications of product and application needs to the design and installation of your conveyor system, we will create a system that works perfectly in your application.