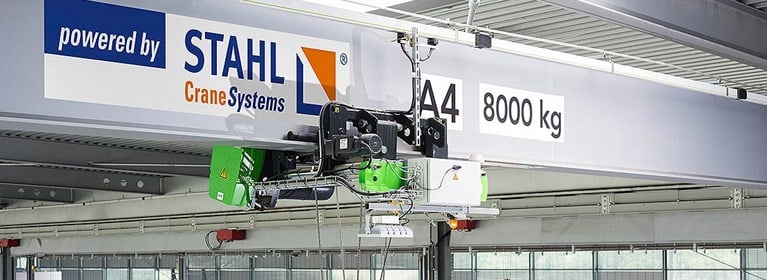
STAHL CraneSystems Provides Custom Solution for Magnet Cranes
Metals Production | Crane Systems | by STAHL CraneSystems | 01 Aug 2016
Magnet cranes enable quick, safe work processes vital to the steel industry. Magnetic lifting beams that pick up steel are usually application-specific depending on material properties, shape, size, and weight of a load. Thus, the corresponding crane system must also be custom designed. Experienced crane-building experts are able to handle these challenging magnet crane solutions that require elevated safety requirements.
Dewald Stahlhandel sells and delivers rod steel across Europe for a wide variety of industries. At its location in Pleidelsheim, Dewald was seeking to expand its range of available products. The company required additional space and a stronger crane. An experienced crane builder was quickly found – Innokran, a partner of STAHL CraneSystems. After an analysis of the processes and requirements, Innokran engineered a crane solution tailored specifically to Dewald's workflow. “We had high expectations for the new crane system and were pleased with the recommendations from Innokran,” says Thorsten Maier, one of Dewald’s managing directors. With an added 1,000 square meters of space and two new magnet cranes, Dewald can now lift components up to 14-tons and offer larger rod steel diameters.
A lifting beam moves long material, but if this lifting beam is too long, shorter parts cannot be safely transported and stored. If, however, the lifting beam is too short, it is not possible to lift long rods safely. If both types of materials need to be transported, it is more efficient to use a two-part lifting beam that can be inclined. In this configuration, either four magnets are available for long objects or just two at different heights for short steel rods. This solution requires a special lifting beam and two hoists that can be controlled independently of one another when necessary.
The two hoists on the crane normally run in tandem mode. A crane operator places the magnetic lifting beam down on the steel via radio remote control, activates the four electromagnets with a button, and the load is held safely. If shorter steel components need to be picked up, the two parts of the lifting beam can be operated independently and moved to different heights with the help of wire rope hoists and their magnets.
Two 8-ton SH series wire rope hoists from STAHL CraneSystems and a magnetic lifting beam from Scheffer operate the crane. “We were able to use CraneKits from STAHL CraneSystems for this special construction. Thanks to our history with STAHL CraneSystems technology, it was easy for us to adapt the components for the special application at Dewald,” says Christoph Fischer. The advantage, he says, is obvious. “The customer benefits from high-quality products and the solution that was specially adapted to his application.”
A second crane with two SH wire rope hoists and crane components from STAHL CraneSystems also runs in the hall. This 12.5-ton crane also serves to move the long steel rods. Its main task is, however, to lift cut steel slices out of the saw. The slices are placed on pallets and then loaded on to trucks by forklift. A special single magnet that is hung from one of the wire rope hoists is used for fastening. The power connection needed for this is located at the load hook. Since the steel slices stand upright after cutting but need to be transported horizontally, the special magnet enables the load being turned in the air.
Installation of the crane system was quick and smooth and both cranes have proven their worth since then in daily operation. There are already plans for the next extension. “We will definitely turn to Innokran again for our next expansion," says Maier.