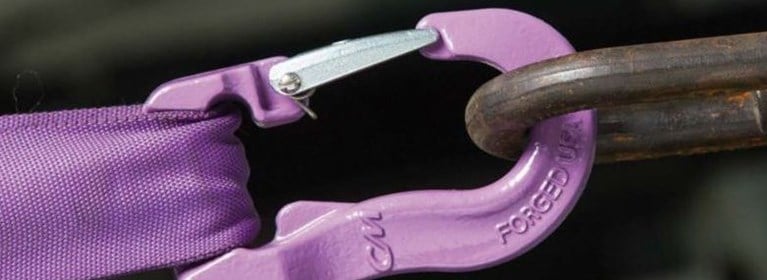
What to Know Before Rigging with Synthetic Slings
Considerations to Keep in Mind When Using Synthetic Slings
Construction | Manufacturing | Rigging | Hoisting & Lifting Equipment | Inspection & Maintenance | Safety and Training | By Rob Bruno | Jul 15, 2020
Synthetic slings are used in a wide range of industries around the world and have become a go-to for many riggers due to their flexibility, lightweight, and ease of handling. The downside? You need to pay extra attention when inspecting and rigging loads.
Frequent Inspections for Synthetic Slings
The first two considerations are related to frequent inspections for synthetic slings. ASME B30.9 requires a frequent inspection to be performed each day or shift before rigging with a synthetic sling. This inspection determines whether your sling is safe for use and ensures a safe, efficient, and compliant lift.
These inspections vary depending on whether you are rigging with web slings or polyester round slings.
Inspecting Web Slings
The frequent inspection for web slings per ASME B30.9-5.9.5 consists of checks for:
- Missing or illegible sling identification
- Acid or caustic burns
- Melting or charring of any part of the sling
- Holes, tears cuts or snags
- Broken or worn stitching in load bearing splices
- Excessive abrasive wear
- Knots in any part of the sling
- Discoloration and brittle or stiff areas on any part of the sling, which may mean chemical or ultraviolet/sunlight damage
- Fittings that are pitted, corroded, cracked, bent, twisted gouged or broken
- For hooks refer to ASME B30.10
- For rigging hardware refer to ASSME B30.26
- Other conditions, including visible damage that cause doubt as to the continued use of the sling
Inspecting Polyester Round Slings
The frequent inspection for polyester round slings per ASME B30.9-6.9.5 consists of checks for:
- Missing or illegible sling identification
- Acid or caustic burn
- Evidence of heat damage
- Holes, tears, cuts, abrasive wear, or snags that expose core yarns\
- Broken or damaged core yarns
- Weld spatter or heat damage that exposes core yarns
- Knots in the round sling, except core yarn knots installed by the manufacturer during the fabrication process
- Fittings that are pitted, corroded, cracked, bent, twisted, gouged or broken]
- For hooks refer to ASME B30.10
- For rigging hardware refer to ASME B30.26
- Other conditions, including visible damage that cause doubt as to the continued use of the sling
Calculating Bearing Stress
Bearing stress is contact pressure between two separate bodies that can be high enough to damage or destroy a synthetic sling. Bearing stress is a quick and simple calculation that is often overlooked when planning a lift.
Bearing stress is increased when the sling is unevenly loaded by a curved surface. When attaching synthetics to connection hardware such as shackles, hooks, eye bolts, master links, swivel hoist rings, and any other devices with a curved radius, you will have bearing stress.
WSTDA (4.7.1.1-4.7.1.3) recommends a bearing stress value of 7,000 Lbs. /in2 during sling loading. Over 7,000 Lbs. /in2 could have damaging effects on your slings such as: tear, punctures, and rips in the sling cover which may expose core yarns, all of which warrant removal from service per ASME.
- Effective Width = Actual Width x .75
- Load Bearing Area = Hardware Diameter x Effective Contact Width
- Bearing Stress at Hardware Connection
When using these products with a flat connection surface there is no need to calculate the effective width since the actual width of the flat connection surface can be used in this bearing stress calculation. There are products designed and engineered specifically for use with synthetic slings. These include the CM Weblok Connector, Flat Eye Rigging Hook, and CM Quick Connect Hooks. You’ll notice all these products feature a flat connection surface for synthetics to eliminate sling bunching, pinching and stress at the connection point.
See Table 4-5 WSTDA RS1 for recommended radii for use with round slings:
Sling Protection
When rigging with synthetics, sling protection must always remain top of mind. Look beyond “sharp edges” or corners that could potentially damage or cut a synthetic sling. What may not look or feel sharp can become so under the weight of a load.
ASME B30.9 -6.10.4 states: slings in contact with edges, corners, protrusions, abrasive surfaces, or connecting hardware shall be protected with a material of sufficient strength, thickness, and construction to prevent damage unless the edges are adequately rounded to a suitable radius in accordance with WSTDA-RS-1 section 4.6, the sling manufacture or a qualified person.
Careful consideration must be taken when selecting sling protection to ensure the lift can be made safely and efficiently. Some of the common sling protection types available are engineered sleeves, engineered pads, metal mesh pads, and magnetic corner protectors. Always remember: what may not look or feel sharp, may still under tension, have the capability of damaging a synthetic sling. Even a round radius of smaller than the recommended diameter should be considered sharp.
In Summary:
- Frequent inspections are required prior to any synthetic sling use
- Be sure to conduct the proper inspection for the type of sling you’re using
- Take the time to calculate bearing stress
- Invest in rigging products designed specifically for synthetics
- Keep sling protection top of mind throughout your lift