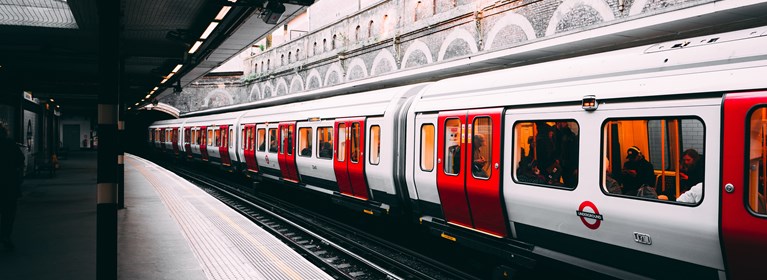
4 Benefits of Electric Actuators you Should Know
How electric actuators stack up against their mechanical counterparts.
Industry News | By Duff-Norton | Oct 11, 2019
Electric actuators are reliable, consistent and robust linear motion devices. When it comes to pitching a new electric actuator to your boss, you will need to navigate around the inevitable barrier of red tape and bottom lines.
Here are four benefits of electric actuators that’ll turn some heads and help you get that all-important green light.
1. Electric actuators are safer. Much safer.
Safety is a primary concern in any process environment. Management doesn’t want injuries on their hands, so when it comes to pitching a new investment in electric actuators, safety is a major benefit.
Compared to their mechanical counterparts, electrical actuators decrease the risk to workers considerably. They don’t require fluid to ensure smooth motion, which reduces the danger of leaks and slippages. They also use acme screw units to hold a load in place, so even in the event of a power outage, you can be sure the actuator won’t slip from its position.
2. They’re completely programmable.
Electric actuators require a motor and some sort of control panel to operate them. In more sophisticated environments, you can program any desired specification and offer a consistent, stable movement, time and time again.
As a result, electric actuators can reduce failure rates and increase productivity. And, should an actuator be reassigned for a different type of movement, they can easily be re-programmed straight from the control system itself.
3. No plumbing = Less maintenance.
If your boss is trying to keep costs down, electric actuators are the way to go. While the initial investment might be higher, you’ll receive a long-term payoff of less plumbing, less maintenance and lower cost of replacement.
Because they don’t require external pumps, they’re also considerably smaller and quieter to work with, meaning they can be deployed in tighter, more enclosed spaces.
4. They’re perfect for low air, low-temperature environments.
Pneumatic and hydraulic actuators use air and fluid to generate movement, while electric actuators use a motor. In colder environments where air is prone to freezing – or in environments without access to air – electric actuators are the safer, more steadfast choice. All you need is a reliable power source.
Automation and integration with smart technologies
‘In the past, it was difficult to gauge how an individual device was functioning or why it was failing because data was limited or maybe not available at all. Now, if an actuator is compatible with Ethernet, it may be able to have its own IP address, so data could be viewed on a web page.’
- Rich Mintz, Marketing Manager at Siemens
The goal of any modern process environment is to be as efficient (and, therefore, productive) as possible. Electrical actuators are built on this principle.
Previously, data about multiple actuators would be fed to a control system. This made it difficult to see the productivity of singular components. Today, however, if an actuator can connect itself to the Ethernet, you could see the performance of a specific actuator and find ways to improve its efficiency.
By using electric actuators – given their ability to be programmed and integrated into a control system – you can begin to build an efficient, connected and productive process environment that is Industry 4.0 ready.
Find out more about our range of electric actuators here.
Contact Our Engineering Team For A Free Application Analysis