Intelligent Steel Handling Equipment and Motion Control Solutions for the Steelmaking Industry
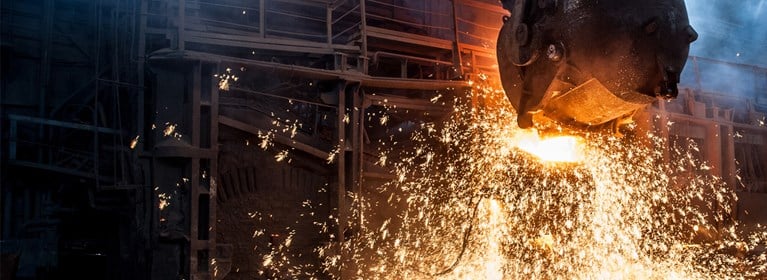
Intelligent motion solutions build safety right into the steel handling equipment, systems, and processes running in the steel mill, helping you keep operators safe and better informed of system status, equipment life, and so much more. We understand the need to work smarter and are committed to developing solutions to help you do just that.
Start The Conversation About Increasing Safety, Uptime, and Productivity In Your Facility Today
From steel production to distribution, our innovative steel lifting technology helps increase your safety, uptime, and productivity.
Crane failure can be catastrophic at temperatures exceeding 2000 F (538°C). That’s why real-time knowledge of the crane’s operation and performance is essential in the harsh melt shop environment inside a steel mill. Maintenance teams need to have information at their fingertips to better predict when equipment failures will occur rather than reacting to unexpected breakdowns, especially when handling molten metal. Drive Support and Diagnostic Tools allow operators to efficiently program, monitor and troubleshoot multiple drives from a remote location outside the hazardous environment. As one-to-one links between the operator and crane, drive diagnostic tools supply critical information such as run, alarm, and fault history; drive trending data; and data analysis.
While in the furnace, impurities called slag float to the surface of the liquid steel. Slag pots located below the scrap bucket collect and channel slag away from the steel. Requiring minimal to no human interaction, fully automated systems perform pre-determined repeatable processes, allowing operators to stay focused on their primary duties instead of attending to multiple concurrent activities while keeping them out of hazardous environments. This helps minimize production backups while enhancing safety and efficiency. Columbus McKinnon’s intelligent solutions combine programmed machinery movement with advanced system monitoring, analytics, and diagnostics, configured to your application needs. IMPULSE® Variable Frequency Drives are the brains behind many of our intelligent motion control solutions with customizable software, specific functions for safety and productivity, and a user-friendly interface.