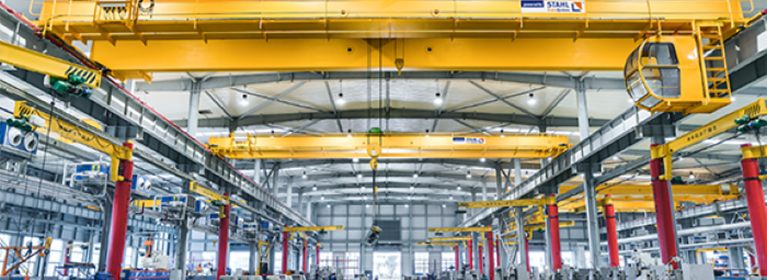
6 Benefits of Overhead Crane Modernization
Automation | Crane Systems | Power & Motion Technology | By Columbus McKinnon | Apr 23, 2021
Overhead cranes are used everywhere. From automotive production facilities to power generation plants, cranes are used day in and day out to keep businesses running. To ensure the highest levels of safety and productivity, while meeting the changing demands of your business, it’s important your cranes are equipped with the latest technology, features, and capabilities.
To do this, you have a few options – buy a new crane, upgrade your existing crane, or repurpose another existing crane that may or may not fit the need. In many cases, it makes the most sense to upgrade your existing crane. Why? Older cranes were often over-engineered and built to last for several decades. When you buy a new crane today, it is hard to get the equivalent.
In this blog, we’ll talk about methods to modernize or upgrade your existing overhead crane to make it more efficient, productive, and safer, and make it last for many years to come at a drastically reduced cost than buying new.
Complete Overhead Crane Modernization: Why Upgrade?
Increased production requirements may demand more capacity, faster operating speeds, more reliable controls, or automation. Reliability may have declined, resulting in unscheduled shutdowns and increased production costs. Inspections may show excessive wear or non-compliance with current safety standards or practices. Parts may be obsolete, resulting in high spare parts costs and long lead times. Imagine the impact an inoperable crane could have on your business while you wait days or even weeks to hunt down a replacement part.
To address these issues, there are six areas where you can make upgrades on your crane:
- Cost-effective structural upgrades
- Mechanical upgrades that extend the life of your crane
- AC and DC crane control technology
- Application-specific variable frequency drive (VFD) firmware
- Radio remote controls
- Automation
Let’s look at these in more detail.
Structural Upgrades
Rather than scrap an outdated crane that is still structurally sound, it is often more cost-effective to upgrade and modify it to meet current operational needs. Since the structural life of an overhead crane can be several decades, increasing the capacity of the crane and runway, moving the crane to another location, or either stretching or shortening the span are options worth considering. You can also look at replacing trolleys with compact trolley hoists that incorporate modern controls.
Mechanical Upgrades
Upgrading old, worn parts with modern and improved counterparts, is another way to modernize your crane. With new technology available, you can extend the life of your crane by replacing a few mechanical components.
For example, modern precision gearing with much closer tolerances can result in reduced vibration, less gear wear, lower maintenance, and notably quieter operation than gears common in older cranes. Utilizing modern flux vector control and eliminating high-maintenance, inefficient hoist mechanical load brakes can improve performance, reduce wear on brake discs or pads, and allow gearing to run cooler. One of the most important considerations for crane modernization, retrofit, or repair is the replacement of outdated or unserviceable crane brakes with current modern industrial braking technology. Modern brakes are designed for easy serviceability, have readily available spare parts, and often fit the existing mounting footprint of legacy brakes, making a drop-in replacement seamless.
AC and DC Crane Control Technology
Control systems are the most important aspect of an overhead crane or hoist, and, without them, the machine would not function nor perform in a safe, reliable, and efficient manner. Many older cranes rely on contactors to control speed and dissipate energy by switching regenerative load currents to resistor banks.
Perhaps no other technological development in the past 40 years has done more to revolutionize overhead crane design than the AC variable frequency drive (VFD). AC VFDs provide greater safety, enhance performance, improve throughput, increase reliability to prolong equipment life, and can help reduce maintenance costs, parts, and personnel.
Training Courses on Crane Drives
Whether you need training on crane operation, installation or maintenance, we have a course for you. We offer a wide variety of courses ranging from overhead crane and hoist inspection certification to mobile crane operator training applicable to professionals in almost any industry. We even offer a NCCCO Certification prep course for individuals interested in NCCCO Overhead Crane Operator Certification.
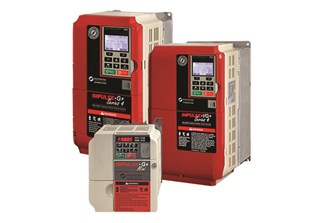
In the case of DC cranes, DC motors are efficient, compact, robustly engineered, and offer year upon year of service, providing acceptable performance for the most demanding applications. Retaining an existing DC motor and upgrading the crane with solid-state DC drive controls is environmentally friendly and provides an opportunity to enhance overall system performance, safety, and uptime while minimizing the risk to production and required capital investment.
Application-Specific VFD Firmware
Simple, innovative, low-cost, application-specific firmware options can be added to VFDs to meet unique application requirements and enhance performance, safety, and production throughput. These technologies include algorithms to prevent load sway, mechanical bucket control for diggers and dredgers, static stepless with footbrake control, and precision crane synchronization technology – to name a few. Because these solutions are integrated into the VFD, an external PLC is not required, leading to a less expensive and less complex control system with fewer failure points.
Radio Remote Controls
Radio remote controls are the most common device used to modernize an outdated crane. There are two places where they are commonly used – in place of pendant pushbutton stations or fixed control stations and cabs. Depending on the location of equipment, pendant pushbutton stations are sometimes inefficient or put the operator in unsafe situations. Pendants keep the operator tethered to the crane, which can limit the operator’s mobility by forcing them to dodge obstacles or avoid pinch points. When it comes to fixed control stations or cabs, two operators are needed to control the crane. Radio controls eliminate the need for two operators, preventing communication errors. It also provides the remaining operator with increased mobility and visibility of the load for increased safety.
With improvements in wireless technology, radio remote controls are safer, ergonomic, reliable, and more flexible than ever. With graphical displays and various types of wireless communication, radios allow operators to view runtime information in real-time and customize control configurations, frequency channels, and security codes from the plant floor.
Automation
Technological advancements in control products and engineering allow us to convert manually controlled overhead cranes, hoists, and monorail systems into modern production tools with extended life cycles. Automation on a crane can be as simple as performing a repeatable motion with the push of a button or as complex as adding multiple keep-out/no-fly zones to a crane bay or incorporating a fully autonomous asset management system. Automation technology, such as off-center pick prevention, snag detection solutions, or auto-dispatch systems, can also be easily implemented to improve the safety, uptime, and productivity of your operations. These solutions allow an operator to work in harmony alongside a semi-automated crane or can fully remove the operator from the process to improve safety and increase throughput. From off-the-shelf automation technology to complete, engineered-to-order automation systems designed to your unique application requirements, the possibilities are only limited by our imaginations.
Overhead cranes represent a significant investment in capital. Therefore, rebuilding and modernizing these assets with new modern parts and electric controls is economically prudent since doing so protects and prolongs the life of these investments, while saving as much as 30 to 40% of the cost of new equipment. It’s far easier and less expensive to maintain a reliable crane than to face unplanned downtime.
Our automated crane systems are designed to improve safety, uptime and productivity in your facility. Not only does crane automation technology allow you to build safety right into equipment with no-fly zones and off-center pick prevention, it also provides you with real-time data and information that enables you to improve operational efficiency and make smarter decisions, faster.
Columbus McKinnon’s Unified and Magnetek brands bring more than 20 years of experience in delivering automated systems to the automotive industry. Our high-technology solutions are featured throughout the automotive manufacturing process, including ergonomic and autonomous workstations like ProPath™ and Intelli-Guide™.
Related Articles
Three Ways Automation Technology Can Improve Your Facility & Operations
Implementing automation in your systems and processes can have a big impact on your facility. Let’s take a closer look at three ways automation can improve your facility and operations.
Do you have technology in place to help you plan maintenance to prevent costly downtime? Do your processes suffer from complexity that causes variations in product quality? Let's take a closer look at three ways automation can improve your facility and operations.
When operating an overhead crane, safety is essential. Whether it's protecting operators from dangerous swinging loads or preventing cranes from colliding with one another, overhead crane safety systems allow you to build intelligence right into your overhead lifting system, helping keep your workers safe and your facility accident-free.
Let's take a closer look at five overhead crane safety systems that can have a significant impact on your operations.