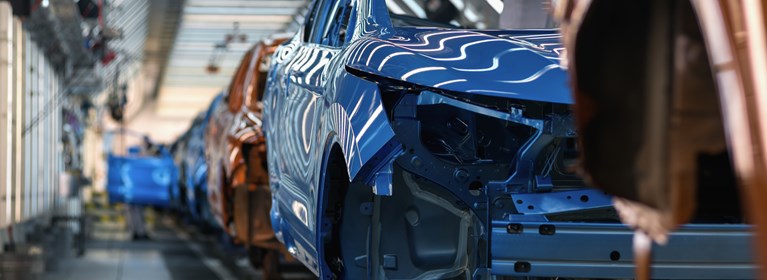
Automotive | Automation | Crane Systems | by Christie Lagowski | 06 Apr 2021
Products: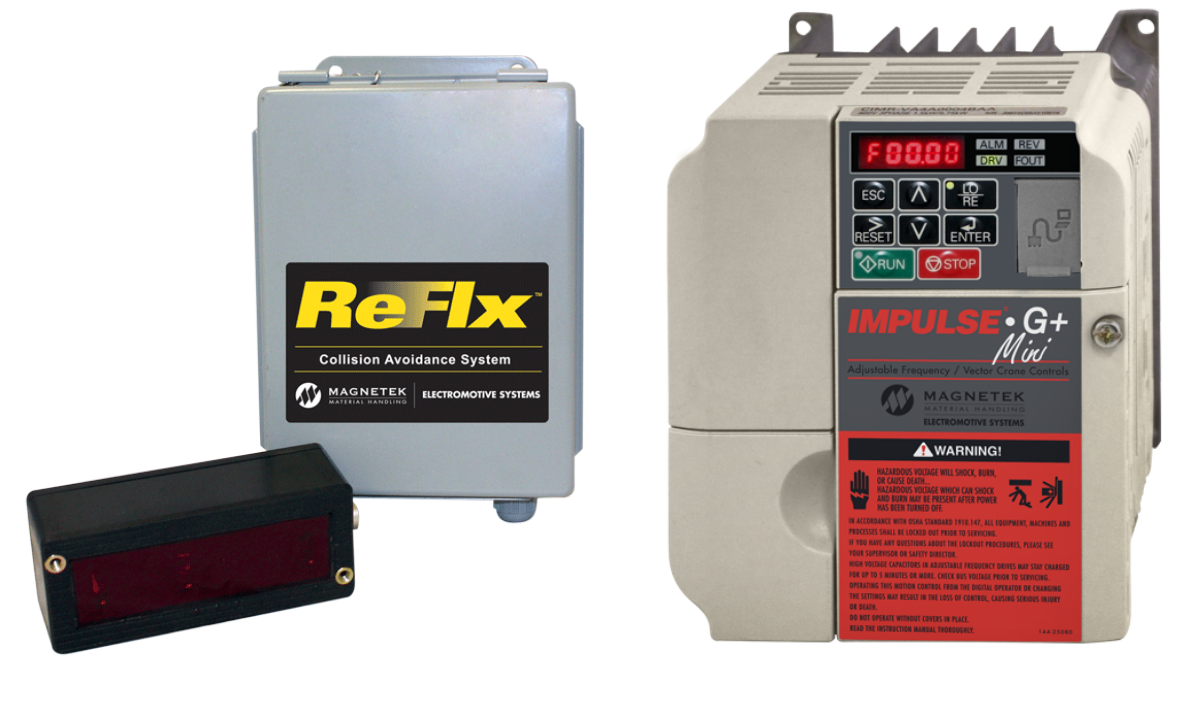
- Magnetek IMPULSE® Variable Frequency Crane and Hoist Controls
- Magnetek ReFlx 120 "Plus" Crane Collision Avoidance System
- Laser Distance Detection Devices
- Programmable Logic Controller (PLC)
- Human Machine Interface (HMI)
- Magnetek Conductor Bar
Challenge:
- Reduce takt time between the engine and transmission marriage
process for a high-production automobile manufacturer - Ensure the correct engine was selected for the incoming transmission
on the production line - Provide sway control technology to ensure safe engine transfer to
the marriage cell
Solution:
- Provided two automated cranes with auto-dispatch technology,
integrating hoist and crane controls, collision avoidance software,
PLCs, HMIs, and power delivery - Reduced takt time by 36 seconds while providing the precision control
and safety the application required - Helped manufacturer increase production from 60 to 72 jobs per hour
In automobile manufacturing, time is money. Every minute saved in the process can move another vehicle off the line and into the market. To increase efficiency and reduce process time, a high production automobile manufacturer needed to reduce the takt time for the engine and transmission marriage process. Specifically, the manufacturer was using a manual marriage cell where several processes had to be performed by a single operator. This included picking hardware, selecting traverse time, marrying two heavy components (an engine and a transmission), and installing a wiring harness and attachment hardware.
The total time needed to do this was 58 seconds — 42 of which were traverse and hardware selection time, while the other 16 seconds were used to install the wiring harness and fasten four bolts. This 58-second takt time was the controlling factor in daily output numbers, which totaled just over 60 jobs per hour, and was unacceptable in this high-production environment.
The manufacturer needed to get total vehicle takt time down to 48 seconds. As an added challenge, the new system also had to ensure the correct engine was selected for the incoming transmission and feature sway control technology to provide safe engine transfer to the marriage cell. Together, these requirements were no easy task.
To meet all the automobile manufacturer’s needs, Columbus McKinnon determined an auto-dispatch system would be the best option to not only reduce takt time but provide the precision control and safety the application required.
Utilizing drives, motors, and automation programming, an auto-dispatch system allows operators to program locations into a PLC or controller, then automatically send the load to different areas within the facility with the push of a button. While the crane is moving on its own, the operator can work on a different task or start on the next step of the production process. These systems can be configured to include multiple locations, depending on application needs.
For this application, two automated cranes were provided to meet the manufacturer’s requirements for 100% uptime. The auto-dispatch system provided:
- Precise horizontal positioning: Laser distance detection devices mounted on the bridge enable horizontal positioning of +/- 1/2”
- Accurate vertical positioning: The hoist motor encoder and the Magnetek IMPULSE Flux Vector Variable frequency Hoist Control work together to control vertical positioning
- Long life: Magnetek IMPULSE VFD crane controls maximize crane performance and reduce wear and tear on mechanical components
- Automated operation: A PLC on each crane provides automatic operation and communication with the Plant MRP system
- Power delivery: Six enclosed-type conductor bars, running the length of the runway, supply power and communication to the cranes
- Easy-to-use interface: Floor-mounted human machine interface (HMI) control station includes a PLC with necessary interface to the process control PC
- Collision avoidance: Cranes are equipped with a Magnetek ReFlx 120 “Plus” Collision Avoidance System. When two cranes approach each other, a primary signal is sent by the collision avoidance system to the on-board PLC to initiate a slowdown of the bridge. As the two cranes continue to approach each other, a second signal is created by the ReFlx system to bring the cranes to a complete stop, preventing contact. As an additional safety measure, a third distance sensor acts a back-up emergency stop in case the primary sensor fails
The auto-dispatch system transformed the manufacturer’s engine marriage crane system into an efficient and safe solution. Process takt time of 58 seconds was reduced to 22 seconds by significantly trimming the time needed to traverse the engine to the cell and safely return it to the work area. Also, the process control PC provided automatic recipe selection and interfaced with other area controllers, helping to ensure correct engine and transmission selection, smooth operation, and quality control.
With the significant time savings, the operator could complete the required task quicker than ever, reducing the production line’s overall takt time, paving the way from 60 jobs per hour to upwards of 72 jobs per hour!
Unified ProPath™
The ProPath Automated Workstation Crane combines our industry-leading Enclosed Track Aluminum (ETA) Rail with “smart” material handling solutions in a unique package to increase the safety, productivity, and uptime of your facility. You can customize each system to match application needs, choosing from an extensive portfolio of crane solutions products, such as variable frequency drives, powered chain and wire rope hoists, radio remote controls, articulating arms, vertical reaction lifters, and much more.
Magnetek® Intelli-Guide™
Combining radios, drives, motors, brakes, and automation programming, Intelli-Guide Auto-Dispatch technology allows operators to automatically send a load to different pre-programmed areas in a facility with the push of a button. Then, as the load moves to the programmed destination along a determined route, the operator can work on a different task or start on the next step of the production process, increasing productivity and efficiency.