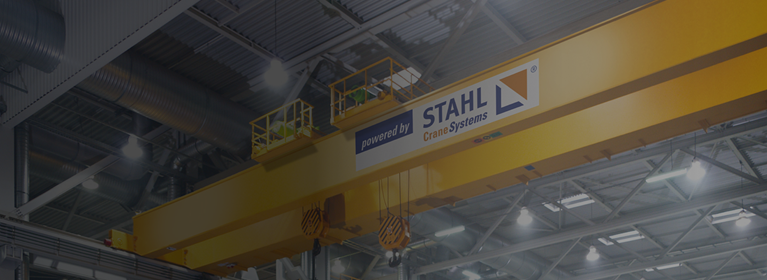
Hoisting & Lifting | Crane Systems | By Columbus McKinnon Training | 05 Feb 2020
Fact: Side pulling is one of the most common and most dangerous mistakes made with overhead cranes.
Overhead lifting operations are a necessary activity in workplaces around the globe. The ability to lift and move material safely is critical to the success of many businesses. Failure to follow safe lifting practices can lead to serious personal injury and cause damage to equipment and facilities.
While there are many aspects to safe lifting procedures, one critical issue I’d like to discuss is crane side pulling and how to avoid it.
Download our guide on how to prevent crane side pulling
Overhead hoists are designed to raise loads vertically.
Accordingly, the load being lifted must be centered under the hoist (Figure 1). Crane side pulling (Figure 2) occurs when attempting to lift any load that is not located directly under the hoist. Another form of side pulling occurs when a crane operator attempts to use the bridge or trolley drives to apply force to move an object horizontally when the load is not first fully suspended on the hoist and free of the floor or other support. Regardless of the manner in which side pull is applied, there are many unintended, damaging and potentially dangerous results that can occur. Side pulling a hoist or crane, in most cases, results in a violation of OSHA regulations, and numerous industry standards.
ASME B30.16, a safety standard for overhead hoists (underhung) states that:
"Hoists shall not be operated unless the hoist unit is centered over the load, except when authorized by a qualified person who has determined that the components of the hoist and its mounting will not be overstressed. Should it be necessary to pick a load that is not centered under the hoist unit, precautions should be taken to control the swing of the load when it is picked clear of its support."
What are the dangers of crane side pulling?
As the load is lifted free of the floor or other support it will attempt to center itself under the hoist, causing the load to rapidly swing in a horizontal arc (Figure 3). This pendulum effect can cause serious injury to personnel or damage to other equipment in the area.
The wire rope or load chain can be forced out of the grooving or pockets on the hoist drum or lift wheel. This can damage the chain/rope, and may also cause damage to drums, sheaves, and other components. In the best-case scenario, this can lead to costly repairs and downtime. More importantly, it could cause the chain or wire rope to break and the load to drop, putting equipment, facilities, and personnel at serious risk.
Side pulling at an angle that is not in line with the length of the bridge or monorail (Figure 4) could cause the trolley hoist to tip, making the trolley inoperable. In the worst case, the trolley hoist could actually be pulled off of the beam. This side pull condition also puts stresses on the beam itself and could cause the beam to skew (Figure 5).
Side pulling is not considered “normal operation” of the hoist and therefore may void the manufacturer’s warranty.
Attempting to lift a load that is located beyond the end of a bridge beam or monorail
(Figure 6) could damage the safety stops at the end of the beam. In rare cases, this has caused the trolley hoist to fall off the end of the beam.
Having worked in the crane and hoist industry for more than 35 years, I am amazed by the number of inquiries that I receive regarding side pulling. These queries may come in the form of a question such as “what is the maximum angle of side pull that is permissible with your hoist?” Customers may also make a statement such as “The distance from my bridge beam to the floor is only 20’ but I need a few feet of additional wire rope on the hoist so I can pull materials out of the adjoining bay.”
These are the GOOD situations, where at least the potential for side loading has been made known and it can be properly addressed. What worries me are the situations where these circumstances may exist but are not made known to the hoist/crane manufacturer or crane service provider.
Intelli-Lift Side Pull and Off-Center Pick Technology
The Intelli-Lift System detects a load misalignment or snag condition and alerts operators with a visible and audible warning before a dangerous situation occurs.
How to Prevent Side Pulling on Cranes and Hoists:
- Make sure that all new crane and monorail systems are designed and installed by qualified material handling professionals.
- Have existing overhead lifting equipment and lifting applications reviewed by a qualified person to ensure these systems are properly located to provide full hook coverage (without side pulling) for all locations where materials to be lifted are located.
- Arrange for hoist and crane operator safety training of all personnel within your organization who may use overhead lifting equipment as well as all managers or supervisors who may direct others to use that equipment.
- Ask your overhead lifting equipment provider about the availability and functionality of devices such as overlay limit switches, rope guides and others equipment used to detect, prevent or reduce the damaging effects of unintended side pulling.
- Consider using an adjustable lifting beam and counterweight to allow an off-center load to be lifted without creating side-pull on the hoist.
Columbus McKinnon Training
Articles authored by "Columbus McKinnon Training" were written by industry professionals with decades of unique and in-depth experience in the material handling industry who are no longer employed by Columbus McKinnon.
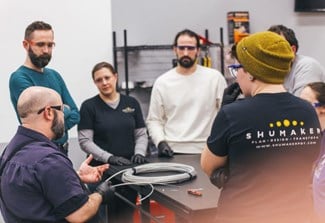
Related Articles
Two prime causes of accidents are overloading and poor rigging. To prevent accidents, we suggest these guidelines:
Pre-planning your lift with everyone involved will ensure proper equipment and personnel are in place to make a safe lift.
A safe working environment is important to everyone, regardless of company, industry or job. Here are the Top 10 Workplace Safety Tips for All Employees.