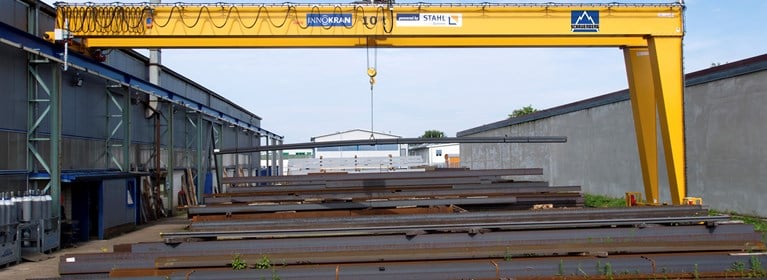
Defying wind and weather - Renewing a crane system for outdoor use
Metals Production | Manufacturing | Crane Systems | Hoisting & Lifting | By STAHL CraneSystems | 27 Oct 2021
With the modernisation of a crane system, Stahlbau Schauenberg increased the logistical capacity of an expanded external warehouse at the site in Ihringen in South Baden. More positive results of the project conducted by Innokran, the crane partner of STAHL CraneSystems, include significant time savings, e.g., when loading and unloading lorries, as well as increased flexibility and enhanced safety when transporting material.
Stahlbau Schauenberg GmbH is a family business that has stood for professional competence, reliability and flexibility since its foundation in 1958. Their focus is on plant construction, as well as industrial and commercial construction. Stahlbau Schauenberg has evolved into an international group of companies with approximately 500 employees worldwide and six sites, three of which are in Germany.
“Our head office is in Kirchzarten near Freiburg. Plant construction is located there for process and refinery furnaces, chemical and petrochemical plants as well as power plants among other things. At the plant in Ihringen, which is about 30 km (18.6 miles) away, around 40 employees carry out the attendant steel construction, e.g., reinforced steel construction, pipe bridges or industrial shed construction. We also have an assembly site in Leipzig,” explains Werner Broβ, production manager at Stahlbau Schauenberg for the plants in Kirchzarten and Ihringen.
Expanded capacities require more power
Crane systems and hoists of STAHL CraneSystems were already being used since 2009 for the handling of steel in Kirchzarten. In the meantime, five projects have been realised in Kirchzarten and Ihringen together with Innokran, the long-standing certified partner of Stahl CraneSystems. The most recent project was the modernisation of a crane system in Ihringen. Up to 5,000 tons of steel are processed there every year, with steel profiles being stored outside. To create more capacity, the external warehouse was expanded by a third in 2019.
Werner Broβ: “Against this background, the old crane with a span of 12.5 metres (41 feet) and lifting capacity of 6 tons was no longer able to meet the new requirements on the larger site. Therefore, we had to rethink the logistical concept and finally decided to modernise using a semi-gantry crane.”
Larger span and higher load capacity
With a span of 19 metres (62.3 feet), the new crane should allow for the efficient transportation of material over the entire outside area and with a load capacity of 10 tons should allow the heaviest of work to be carried out. As with a similar project in Kirchzarten, Stahlbau Schauenberg decided on a hoist with an SH 50 cable from STAHL CraneSystems with low starting and construction height dimensions.
“Being specialists in steel construction we took on the corresponding adjustments to the crane tracks. To do so, we only had to replace the crane girders on the stilted crane track on the shed side and extend the entire crane track by 24 metres (78.7 feet). The elevated crane track was however completely removed and a new, longer crane track was aligned on new foundations on the ground,” according to Werner Broβ.
Design measures maintain existing crane track
Basically, the shed-side crane track for the planned larger crane was not designed to accommodate the horizontally acting guiding forces when accelerating and braking. “For this reason, we have fitted horizontal guide rollers to the lower ground-side crane track of the portal supports to relieve the upper crane track, so as to eliminate the track guiding forces. The entire crane construction, including crane bridge, was specially designed to be particularly rigid. Further features of the crane are the additional drives, wind protection and standstill heaters,” reports Christoph Fischer, Managing Director and Crane Specialist at Innokran.
Reliable and safe even during strong winds
Outdoor cranes in particular always have large areas for wind to affect and also have to withstand strong wind forces. This is even more the case when heavy loads hang on the hook. Therefore the entire statics of the new semi-gantry crane is designed accordingly at Stahlbau Schauenberg. In addition, the crane has four drives instead of two, so that safe operation is possible even at wind force 7, i.e., wind speeds of up to 15 m/s (49.2 ft/s). And even if the crane system is not in operation, it must be secured against strong winds and even storms despite the trolley brakes being closed. Wind protection with electrically adjusted safety bolts is therefore located between the drives.
Worthwhile investments in additional protection
In addition to strong winds, cranes for outdoor use are always exposed to a wide variety of other weather types. There is always the problem of corrosion and the buildup of condensation, in particular in the switchgears and engines due to changing temperatures. For this reason, the control cabinet attached to the side of the crane bridge is made of stainless steel. The double-rail crab is protected from rainfall by a special roof construction. All switchgears, engines and hoists as well as crab trolleys and crane trolleys are also equipped with standstill heaters. From the point of view of production manager Broß, this is a worthwhile investment: “In the winter of 2020/21 we had already had heating systems in operation for some time.”
Enormous time savings for loading and unloading
The new semi-gantry crane at the Ihringen site has changed a lot. This not only means that the expanded storage capacities can be optimally exploited by the larger sized crane. According to Werner Broß, there are advantages: in particular the huge time savings and increased flexibility when transporting material. Among other things, the maximum speeds of the hoist [8 m/min (26.2 ft/min)], crab trolley [20 m/min (65.6 ft/min)] and crane trolley [40 m/min (131.2 ft/min)] contribute to this. “A decisive factor for us, however, was above all the maximum load capacity of 10 tons and the maximum lifting height of 7 metres (23 feet).”
Due to the expansion of the external warehouse, the lorries no longer have to manoeuvre awkwardly as before, to reach the site. This saves time, also when loading and unloading with the new crane, as Werner Broβ emphasises. “We are no longer forced to rotate the material for transport by 90 degrees and manoeuvre past the shed-side supports, but can use nearly the entire span of the crane, to process the steel profiles in parallel at an average length of 16 metres (52.5 feet).”
More flexibility through greater lifting height
The loads to be handled are also increasing, according to the production manager, as the individual weight of the profile containers delivered has increased in weight in recent years. “With the old crane, we had to split the loads or pick up steel girders individually. Due to the higher load capacity of 10 tons we are now in the position to lift containers completely. This also saves us an enormous amount of time. And since the hoist is equipped with a load spectrum recorder for monitoring the most important parameters, including the maximum load, lifting, transporting and lowering of loads is particularly safe.”
In addition to considerable time savings and an increase in safety, the new gantry crane also provides a greater degree of flexibility, not least due to its lifting height of 7 metres (23 feet). “Now, even with lorries with tarpaulins, we can lift the loads over the side walls, instead of laboriously unloading the steel profiles or containers over the back of the loading area, as in the past.”
Significant increase in safety and freedom of movement
The gantry crane is operated by radio remote control with protection type IP65. Its receiver, located in the switching cabinet on the crane bridge, is protected against the effects of weather. An external antenna mounted on the control cabinet transmits the radio signals.
For the crane operator, the handy radio remote control not only means more comfort. It significantly increases safety when transporting loads, as Werner Broβ knows only too well from daily experience: ”The operator can control the crane from a safe location and is not forced to climb over steel profiles when moving over the site with the load, as with cable-based systems. He has therefore complete freedom of movement during his work and can always choose the safest way to the hanging site.”
Satisfactory results with a positive conclusion
In view of the consistently good experiences when working with Innokran so far, production manager Werner Broβ is also extremely satisfied with the direction and results of this project: “We are saving a lot of time and costs when loading and unloading and transporting profiles over the outside areas. In addition, the new gantry crane has made us much more flexible in many respects. Six months passed from placing the order to commissioning the gantry crane. We did not have to accept any major restrictions during this time, because we could continue using the old crane during construction work. Finally, thanks to the current crane, we dismantled the crane track that was no longer needed and removed the other crane components.”
By renewing the crane system, Stahlbau Schauenberg increased the logistics capacities of an expanded external warehouse at the site in Ihringen.
The double-rail crab is protected from rain by a special roof construction. All switchgears, engines and hoists as well as crab trolleys and crane trolleys are also equipped with standstill heaters.
(Picture: Innokran GmbH)
The new lorry entrance to the outside area. The gantry crane now saves a lot of time and costs when loading and unloading and transporting the profiles in the outside area.