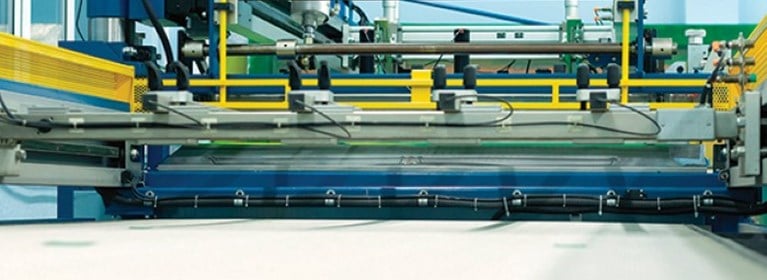
Hydraulic vs. Electric Linear Actuator: Which is Best?
By Duff-Norton | 20 Dec 2022
When buying a linear actuator, it’s important to choose a product that will fit best with your application and specific demands. Whether you want a high load capacity, a longer duty cycle or something that requires very little maintenance, you’ll need to research each ‘type’ of actuator thoroughly.
In this post, we’ll discuss the advantages and disadvantages of two of the most popular types of linear actuators – hydraulic and electric – to help you find the perfect device for the job.
What is a hydraulic linear actuator?
Hydraulic linear actuators use fluid and pressure to provide movement and apply force. They have a high-power density which enable small package sizes that provide a high load/thrust capacity from a relatively small cylinder. However, system design and cost must also be considered because of the need for auxiliary components to provide pressure, such as motors, pumps, filtration, hoses, and couplings. Pressurized systems also tend to have higher long-term maintenance costs due to the need to contain the integrity of the system for seals, leaks, or other issues that may arise.
These actuators are powered by pumps of incompressible oil. The pressure that the fluid creates moves the cylinders and, in turn, helps move your application.
Pros
- Load capacity. Unlike electric linear actuators, hydraulic actuators are suited to high-force applications and are customizable to almost any weight. They are also the most powerful actuator on the market and are suitable to work under heavy pressures.
- Convenience. The external pumps and motors for this type of actuator can be placed a reasonable distance away from the application without affecting the power supply.
- Constant pressure. Due to the incompressibility of liquid, a hydraulic actuator can hold constant force without the pump having to supply more pressure.
Cons
- Leakages. These actuators require expensive plumbing, maintenance and continuous checks. Due to the nature of the product, the likelihood of oil leakages is high. Additionally, high temperature environments can cause damage to the product if not monitored diligently.
- Components. Hydraulic linear actuators are not contained and require numerous external components. If you’re looking for a small device, these may not be the best for your needs.
- Speed. These devices are hard to control accurately and may suffer from ‘stick slip’. Put simply, this is where a linear actuator jolts and jerks in the transition between being still and moving.
- Cost. Although the cost of the initial components is relatively low, the cost of installation and maintenance can be pricey. Unfortunately, if you want your hydraulic actuator to run smoothly, the cost of regular maintenance is a necessary price to pay.
What is an electric linear actuator?
Electric linear actuators, also known as electromechanical actuators, convert torque to linear displacement (travel and force). They are mechanical components that use electric motors coupled to machine or ball screws and gear sets to provide mechanical advantage. There are many combinations available to supply a wide range of speed and load requirements. These actuators are available with many standard features and numerous options, such as limit switches, position feedback, and more to ensure they can fit a wide range of application needs. While electric linear actuators may have a higher upfront cost and require a larger footprint to install (since they include the motor and mounting), they are easier to maintain and have lower long-term maintenance costs. When sized properly, they are durable and ensure long product life.
Unlike the hydraulic variant, these linear actuators are powered exclusively by motors. The motor powers the lead screw, which is fitted with a nut that runs up and down the thread. This converts the rotary motion into linear movement.
Pros
- Precision and speed. This actuator offers repeatable capabilities with easy, automatic operation controls. The speed of the device is also easily controlled and smooth.
- Less maintenance. As there’s no risk of fluid leakages, there’s very little requirement for regular maintenance. This, of course, reduces costs and increases productivity for both the application and your team.
- Quick installation. Setting up electric actuators only requires simple wiring, meaning you can install your device quickly and cheaply.
- Load holding and safety. Most electric actuators contain acme screw units (or fail-safe brakes) which are self-locking in the event of a power failure.
- Contained. These actuators don’t require external pumps or motors and are therefore much smaller and take up less space.
Cons
- Unsuitable environments. Although these actuators will perform well in most environments, installation in hazardous or flammable areas requires the use of equipment rated for these conditions. Only actuators specifically created for use in environments where flammable or explosive gases or particulates are present should be used in these applications. This is necessary in order to prevent injury or damage.
- Overheating. If left running for too long, or over the specified duty cycle, electric actuators may overheat and reduce efficiency.
- Cost. The initial cost of purchasing an electric actuator is high. However, the running and maintenance costs after this are significantly lower than that of a hydraulic actuator
Why would you use an electric linear actuator?
Electric linear actuators allow for precise motion control. While fluid (also known as hydraulic) valves have improved over time, they are not as precise as a motor. Also, if your application has specific needs, such as harsh environment (washdown and sealing options) or requires explosion proof equipment, electric linear actuators are available with options that meet these classification requirements.
Which is best for you?
Although both variations create a reliable and powerful linear motion for your application, each have their own advantages and disadvantages. So when making your decision, pick the right actuator for your application, specifications and environment.
At the end of the day, making the wrong choice can only cause more hassle in the future, so if you need more guidance to inform your decision, get in touch with a professional who can advise you further.
Duff-Norton
As a leading engineering manufacturer of reliable industrial lifting and positioning products, Duff-Norton is comprised of individuals with in-depth industry experience. Articles authored by Duff-Norton belong to a collection of blogs written by product and application experts throughout the organization.
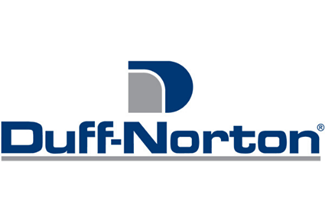