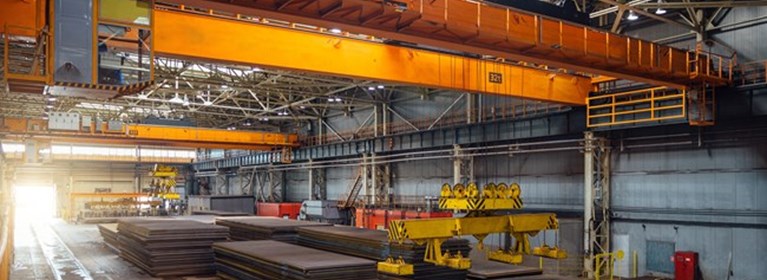
Innovations in Crane Technology
Automation | Power & Motion Technology | Hoisting & Lifting | By CMCO | Mar 24, 2023
In the 19th century, the industrial revolution led to a number of innovations that laid the foundations for modern cranes, starting with Ludwig Stuckenholz in Germany in 1830. Electric overhead cranes, however, were not invented until 1876 in England. Sampson Moore, a Liverpool engineer, invented the first crane of this type for the Royal Arsenal in London's Gun Factory. In the early days, electric overhead cranes were used to lift guns, ammunition, and explosives. Soon after, electric overhead cranes became widely used in industrial applications, particularly in steel mills.
Over the years, there have been numerous innovations for overhead cranes, such as high-capacity winches, electrical control systems, and mass-produced electric hoists in 1910. Many of these innovations were driven by increased demand for cranes, especially after their heavy use in military and shipbuilding operations during World War II. Some of these advanced technologies included introducing remote-controlled and hydraulic cranes. As computer technology advanced in the post-war period, cranes became increasingly sophisticated with advanced safety and control systems.
The development of crane technology
1898: The first large, electric gantry crane is manufactured. It has a load capacity of 12.5 t with a wingspan of 11.5 m.
1964: The first complete range of standard cranes is developed. Typing and standardization enable rational production at a high level.
1984: Introduction of the KT 2000 small crane system. This sophisticated modular system of rails, hoists, chassis, etc. can be used flexibly for simple applications and for automated material flow solutions.
1991: Capacity doubling at the Ettlingen crane plant through innovative process technology.
2006: A new era begins. Innovative crane technology with a practical conductor line, i.e. without movable cables, is introduced to the market.
2010: The new concept, Crane Kits for crane builders, keeps the planning effort manageable and makes order processing effective and economical.
2013: Introduction of the small crane systems KS and KA.
Automation Solutions
The crane industry has undergone a significant transformation due to the rapid advancement of automation technology. Modern crane systems now employ a wide range of intelligent systems and sensors to improve safety, uptime, and productivity. Automation technology allows you to build safety right into equipment with no-fly zones and off-center pick prevention. It also provides you with real-time data and information that enables you to improve operational efficiency and make smarter decisions, faster. Access to real-time data through crane automation systems allows you to better plan for maintenance, predict equipment failures, identify needs for operator training, and monitor multiple pieces of equipment within a facility.
In 2020, Columbus McKinnon introduced the Intelli-Crane™ family of customized automation solutions. These intelligent automation systems are designed to increase common crane applications' safety, efficiency, and productivity, including off-center pick detection, no-fly zones, auto dispatch capabilities, diagnostic analytic technology, and more.
Take a closer look at some of our crane automation solutions.
Intelli-Protect® No-Fly Zone Technology
The Intelli-Protect® system provides no-fly zone technology that can help minimize the risk of accidents, enhance the safety of personnel and equipment, and boost facility throughput. This system uses motion control products, including variable frequency drives, limit switches, and sensors, to slow down or stop cranes in designated areas. With a wide range of options available, from simple two or three-sided setups to more intricate systems with up to 31 protected areas, the Intelli-Protect system can be installed on new or existing crane applications.
Learn More About Intelli-Protect
Intelli-Lift® Off-Center Pick, Snag Detection, and Correction
Intelli-Lift® is designed to ensure the safety of your employees and equipment while lifting loads. It can detect misalignment or snagged conditions and alert operators with a visible and audible warning before any hazardous situation arises. The system uses sensors and a status control enclosure and activates lights and a warning horn if a side pull or off-center pick is identified. This allows for quick correction of the misalignment or snag, either manually or automatically, preventing any dangerous situations from occurring.
Intelli-Guide™ Auto-Dispatch Technology
The Magnetek-brand Intelli-Guide system, featuring auto-dispatch technology, is a powerful tool for enhancing productivity in a facility. By leveraging radios, drives, motors, brakes, and automation programming, this technology empowers operators to program locations into a PLC or controller and seamlessly dispatch cranes to different areas in the facility with just the push of a button. While the crane is in motion, operators can focus on other tasks or proceed to the next step of the production process. These systems can be customized to accommodate multiple locations depending on specific application requirements.
Learn More About Intelli-Guide
Intelli-Connect™ Mobile: Wireless Drive Monitoring, Analytics, and Configuration
Columbus McKinnon's comprehensive diagnostic solution facilitates easy programming, maintenance, monitoring, and troubleshooting of your crane system. Intelli-Connect Mobile’s advanced diagnostics provide crucial information like motion and positioning, equipment status, and energy usage, ensuring that your system and products operate efficiently. The technology provides this information in real-time to your laptop, tablet, or HMI, allowing you to manage equipment from anywhere in your facility, 24/7. The accessibility of this diagnostic data enables faster issue resolution, improved maintenance planning, and ultimately minimizes downtime.
Learn More About Intelli-Connect Mobile
Columbus McKinnon offers a wide range of crane and hoist application-based software that complements the Intelli-Crane family of automation products, such as sway control and drive synchronization. This software can be utilized as a standalone solution or combined with Intelli-Crane automated systems to provide an all-inclusive automation solution tailored to your specific application requirements. Whether you need to protect valuable assets and personnel with zone protection technology or increase productivity with fully automated crane solutions, Columbus McKinnon is here to help you through every step of the process.
Related Articles
If you own or operate an overhead crane or jib crane, you will understand the importance of a regular maintenance program. An overhead crane inspection sheet can be incorporated at any worksite that uses an overhead crane to handle materials. This ensures the system will continue operating properly before a worker handles it. Since operating cranes can be extremely dangerous, it's important to have a comprehensive preventative maintenance program that includes a daily inspection.
Incorporating automation can have a significant impact on a facility. Not only can automation help increase productivity and maximize the uptime and performance of operations, but it can also improve product quality, increase energy efficiency, and provide numerous safety and health benefits. When people think of automation for cranes and hoists, they often think of automating crane and hoist movement in a facility. But, there is another important benefit automation technology can provide – the ability communicate directly with the hoist or crane as well as collect, monitor, and analyze performance data.