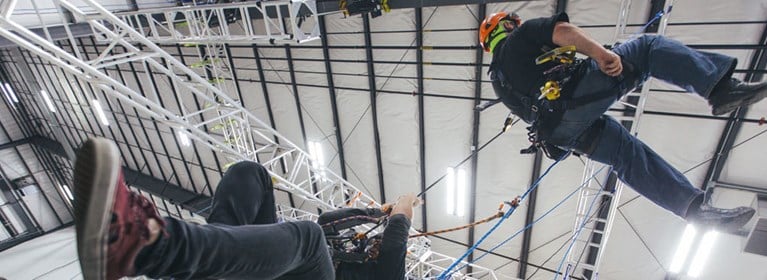
Rigging Manufacturing: Why Forge Parts Versus Cast?
Rigging | Safety and Training | By Troy Raines | Feb 03, 2016
Jason, a product engineer and recent rigging safety webinar attendee, asks:
“Why or when would a rigging equipment manufacturer choose to use the forging method versus the casting method?”
Troy Raines, Chain & Rigging Product Engineering Manager at our CMCO Chattanooga Forge Operations, responds:
Please be patient with me, as I use the word “mold” as a general reference to all tooling used in both the casting and forging processes.
The forging method is appropriate when a manufacturer is:
- (To a large extent) making solid parts. Forged parts can have open sides, through-cavities and pierced holes; however, certain design considerations, such as a draft angle for mold release, have to be taken into account.
- Producing high quantities of parts when an investment in tooling can be justified.
- Needing smaller, lighter parts. Parts can be smaller and lighter due to increased strength, toughness and ductility.
The casting method is appropriate when a manufacturer is:
- Concerned about high tooling costs or a large mold inventory. Cast tooling is less expensive and disposable.
- Looking to eliminate draft angles. Draft angles are incorporated in the mold to allow the part to be removed from the mold. With casting, the mold can be considered disposable or sacrificial. So, because the mold will be destroyed, it eliminates the need for draft angles. Cast tooling is also cheaper, but it only makes one part before being sacrificed.
- Minimizing required secondary operations because casting allows manufacturers to start closer to the finished shape.
Conclusion
Forged parts are always better for rigging equipment because of their part size (same strength from a smaller part), weight, strength, toughness and ductility properties. Cast parts are larger, heavier, weaker, more brittle and require more expensive inspection techniques due to the probability of internal defects. Unfortunately, many rigging manufacturers have resorted to cast rigging hardware because they have hammer size limitations. For years, even Columbus McKinnon has limited the size of its rigging hardware because of its desire to only have its name on forged rigging products.
Expanding its line of high-quality, forged rigging hooks, Columbus McKinnon now offers high-capacity rigging hooks with capacities ranging from 31.5 - 60 tons. Our high-capacity hooks are well suited for heavy-duty lifting applications with features such as a 5:1 design factor; ultra-strong, forged latch tab, quenched and tempered material for maximum strength; and highly visible load rating marking for easy identification.
Additional Resources:
View our Safety Webinar: The Forging Process – Manufacturing Heavy Duty Hooks
Troy Raines
Troy Raines is Columbus McKinnon’s Chain and Rigging Product and Engineering Manager. He joined the company in 2005 as a general engineer, supporting quoting specials, product design, and manufacturing engineering initiatives.
Today, Troy plays a key role in the development and support of rigging products and contributes to several major industry standards. He is a member of the ASME B30.9 (Slings), B30.20 (Below-the-Hook Lifting Devices), and BTH-1 (Design of Below-the-Hook Lifters) committees. He also serves as an alternate on B30.10 (Hooks) and B30.26 (Rigging Hardware), and is active on multiple Web Sling and Tiedown Association technical committees, as well as ISO/TC 111/SC1 and SC3.
Outside of work, Troy is proud of his military service and his role as a father to three sons.
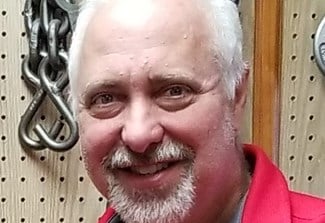