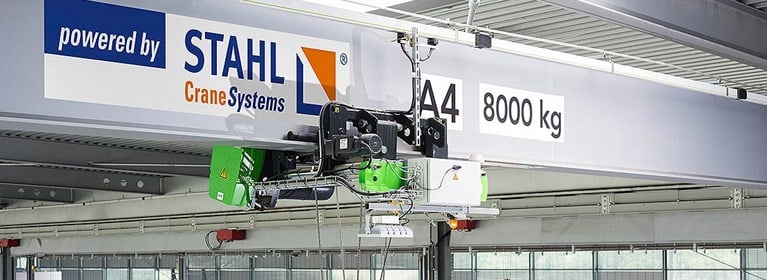
STAHL CraneSystems Supports Major Power Station Project in the Himalayas
Power and Utilities | Construction | Hoisting & Lifting | Crane Systems | By STAHL CraneSystems | Jan 26, 2018
As tourism in India continues grow, the country is investing in projects to meet the demands of increased visitors. One of the projects was the Kishanganga hydroelectric power plant between the border of Pakistan and India. Kishanganga is part of a large hydroelectric power station program being implemented by the state-owned Indian power utility NHPC Ltd.
The Kishanganga hydroelectric power plant lies 2,400 meters above sea level. At these altitudes, temperatures from November to May are very cold. In the summer months, by contrast, landslides make the region difficult to access. For these reasons, among others, NHPC Ltd. sought strong partners for the project that could guarantee punctual delivery and reliable work. DSD NOELL GmbH from Würzburg and STAHL CraneSystems from Künzelsau stood up to the challenges of these high requirements.
To ensure continuous operation of the power plant’s turbine generators, which are meant to generate a total of 330 megawatts of electricity, it is vital to ensure a continuous flow of water. The plan to guarantee this – dam the Kishanganga River. As a specialist in the field of hydraulic steel structures in waterways, weirs and hydroelectric power stations, DSD NOELL GmbH planned and built a 37-meter-high weir. STAHL CraneSystems, a specialist in crane technology with the largest range of high-quality hoisting technology available worldwide, developed and delivered the winch system to lower the 100 ton sluice.
The demands on the hoist were high as it had to work reliably in the adverse environmental conditions of the mountainous region. The first concepts for the custom solution were developed at the headquarters of STAHL CraneSystems in Künzelsau in 2009. The solution was a stationary SHW 8 winch with a safe working load of 2 x 60,000 kg consisting of two rope drums and a gearbox. To ensure equal weight distribution, the hoist was designed in reeving of 2 x 12/2-1 and the drum manufactured in a length of L4. The final height of lift achieved after completion was 21.5 m at 2 x 150 m rope length. Thanks to double symmetrical arrangement of the reevings, it was possible to realize perfect synchronism of the two load hooks. The total length of the winch system covers almost 9 meters.
The rope drums are flanged to the gearbox with special couplings, thereby compensating all tolerances between the machine and steel structure. Due to local conditions, the gear motor is mounted vertically. As a result of this unusual assembly, the hoist motor is mounted above one of the two rope drums.
Safety is paramount
To ensure safe lowering of the sluice, the engineers from STAHL CraneSystems implemented the rope with seven-fold safety. In addition to that, they included a second brake in the winch system as safety brake, flanged directly on to the gearbox. The hoist was equipped with an overload cut-off device for each of the two load hooks and placement of the load realized separately through slack rope cut-off for each of the two hooks. Both hook positions are shown on a display on the switch cabinet doors. In addition to that, the motor currents of the hoist motor are shown on ammeters. This hoist motor is additionally protected by motor circuit-breakers.
The hoist is designed for operation in ambient temperatures between –25°C and +40°C. Robust, pole-changing technology with further tolerance ranges enables operation in unstable mains power supplies. An external ventilation with stopping control was implemented in the hoist motor to ensure a 15-minute duty for the hoisting technology with a subsequent cooling phase. The winch system was given a special finish, a 270 µm thick top coat of polyurethane, to make it weatherproof. Due to the air humidity, STAHL CraneSystems also equipped the panel boxes and hoist motor of the individual hoists with a heater.
A hoist brake with built-in brake venting lowers the load with pauses in the event of a power failure. The weight of the load is determined continuously by the SMC multi-controller via analogue measuring sensors. In the case of an overload, the lifting movement is immediately switched off. The multi-controller can, moreover, measure further data such as the load spectrum, operating time, full-load operating time and motor switching operations and read them out with the help of a PC.
Putting the technology to the test
The performance of the winch was put to test at Haslinger GmbH Metallbau + Krantechnik, a certified partner of STAHL CraneSystems, in September 2011. With its “partner of” concept, STAHL CraneSystems has been pursuing a strategy of separating crane building and crane technology from each other. Under this model, competent crane builders handle the planning and production of crane systems, while STAHL CraneSystems concentrates on the development and production of hoists and crane technology.
With that said, Haslinger GmbH Metallbau + Krantechnik manufactured the steel portal, including ladders, walkways, the framework for the winch systems and the enclosure for the hoisting technology. Following successful testing, the hoisting technology and crane system were transported to the installation site.
The crane system was commissioned on-site by the STAHL CraneSystems factory service center. Once delivered, the sluice was lowered with the help of the special winch. The Kishanganga hydroelectric power plant was set to go online in 2018.
Test set-up of the SHW 8 special winch from STAHL CraneSystems: the gear motor was mounted vertically and the hoist motor above one of the two rope drums.
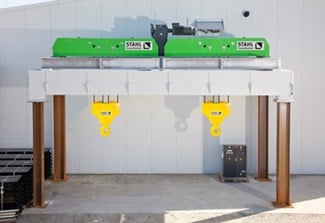
Yesterday building site, today dam – work on the Kishanganga River in the Himalayas.
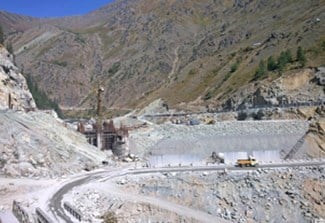