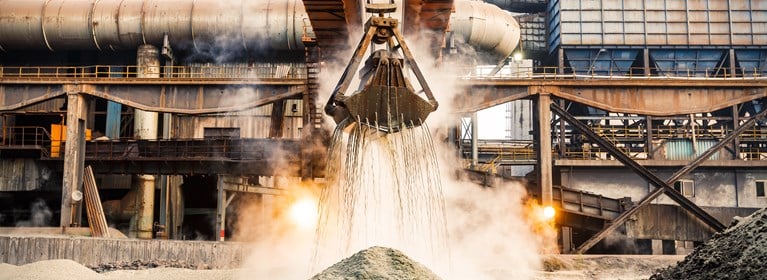
Metals Production | Manufacturing | Sistemas de grúas | Tecnología de potencia y movimiento | | 23 sep. 2020
PRODUCTOS Y SERVICIOS:
- IMPULSE®•G+/VG+ Serie 4 Variadores de frecuencia
- Software IMPULSE®•Link con acceso inalámbrico
- Control avanzado del cucharón Software a medida
- Resistencias de frenado dinámico
- Controlador lógico programable (PLC)
- Interfaz hombre-máquina (HMI)
- Servicios de la División de Automatización
Desafiar
- Desarrollar una solución automatizada para reemplazar los controles operados manualmente
- Habilite un programa de limpieza consistente para el clarificador de fosa de incrustaciones
- Reduzca la dependencia de los controles manuales
- Proporcionar un proceso más eficaz para filtrar el agua de las incrustaciones de los molinos
Solución
- Solución totalmente automatizada instalada que limita la participación humana en áreas peligrosas
- Movimiento constante y preciso para una limpieza eficiente de los pozos de incrustaciones
- Comunicación inalámbrica integrada para análisis y diagnóstico continuos del sistema
- Mejore la seguridad, el tiempo de actividad y la productividad con software especializado específico para grúas
Una instalación siderúrgica descubrió que su clarificador a base de molino era ineficiente, lo que ocasionalmente causaba daños en el equipo e interrupciones en el proceso de producción. La cascarilla de molino es un subproducto del acero refrigerante por chorros de agua. Un sistema de grúa clarificadora separa la cascarilla de molienda del agua, la recoge en pilas y retira el producto para su reventa. Luego, el agua restante se trata y se redirige para los procesos dentro de la acería. El sistema necesitaba ser actualizado para que este proceso funcionara sin problemas.
VER TODOS LOS VARIADORES DE FRECUENCIA IMPULSE®
El sistema de grúa original utilizaba controles de contactor obsoletos y era operado manualmente por técnicos, lo que los alejaba de sus tareas principales. Debido a la falta de monitoreo del sistema, las pilas de sarro acumuladas se desbordaron en el área exterior e interfirieron con el movimiento de la grúa. La acumulación de sarro en el agua reciclada también obstruía las boquillas de pulverización dentro de la planta siderúrgica y causaba un mantenimiento costoso y lento.
El equipo de automatización pudo diseñar una solución automatizada innovadora para mejorar la seguridad, el tiempo de actividad y la productividad de la planta siderúrgica. El nuevo sistema incluía paneles de control completos, variadores de frecuencia de la serie IMPULSE®G+ y VG+ de la marca Magnetek® con software personalizado específico para grúas, resistencias de frenado dinámico e integrado un controlador lógico programable (PLC) y una interfaz hombre-máquina (HMI) basada en PC. todos los cuales se conectaron a través de la comunicación Ethernet para informar análisis e información de diagnóstico.
Programado para iniciar ciclos automáticos en momentos específicos, el nuevo sistema de clarificación de fosa de báscula fue diseñado para completar controles de seguridad y garantizar que se cumplan todos los parámetros antes de que comience la operación. Si no se cumple algún parámetro, un técnico puede acceder a la HMI que muestra información del sistema para determinar qué parámetro está impidiendo el funcionamiento. La HMI, así como las computadoras adicionales y el equipo de monitoreo, están ubicados en una sala de control fuera de la grúa, lo que proporciona un centro de operación para los técnicos y permite el acceso remoto cuando sea necesario. El software IMPULSE®•Link, que permite una fácil programación, monitoreo y resolución de problemas para múltiples variadores de frecuencia, ayuda a garantizar que la grúa permanezca en funcionamiento al mostrar información analítica y de diagnóstico en la HMI en la sala de control.
Una vez que se completan los controles de seguridad, la grúa clarificadora abandona su posición estacionada y se mueve al depósito designado de la cascarilla de laminación. Para determinar la secuencia de limpieza, el codificador de elevación mide la altura de las pilas de básculas en cada punto de recogida y regresa al punto más alto una vez que se han medido y registrado todos los puntos de recogida, omitiendo cualquier punto que ya esté por debajo del punto de ajuste de profundidad limpia. El polipasto, controlado por los variadores IMPULSE•VG+ Serie 4 de la marca Magnetek, baja un cucharón al foso de la báscula hasta que se detecta una condición de cable flojo. La función de medición de la altura del gancho de los variadores IMPULSE utiliza una señal de codificador incremental para determinar la altura del gancho desde una posición calibrada. El software de control del cucharón incorporado en cada impulsor controla los diversos movimientos del cucharón y proporciona a los operadores el estado de apertura/cierre del cucharón, incluso cuando está bajo el agua.
Los movimientos del carro y del puente, controlados por los variadores IMPULSE•G+ Serie 4 de la marca Magnetek, utilizan codificadores absolutos para el posicionamiento, lo que facilita el traslado de la báscula a la zona de descarga para su recogida y retirada. El sistema controlado por computadora monitorea los depósitos de sarro en el área de descarga para que la grúa pueda seleccionar automáticamente una ubicación de descarga, seleccionando una ubicación diferente cada vez para minimizar la cantidad de sarro en cada ubicación. Las pilas se recogen en tamaños más consistentes y manejables, lo que ayuda a minimizar las obstrucciones para la grúa y garantiza una fácil eliminación.
Integrada con los variadores IMPULSE, la comunicación Ethernet requiere menos cableado en el sistema, permite el acceso remoto para ajustar los parámetros y simplifica la programación de los PLC. Para ayudar con la puesta en marcha, los ingenieros accedieron al sistema inalámbrico de forma remota desde las instalaciones de Magnetek en Menomonee Falls, Wisconsin, para ajustar el software para que se ajustara a las necesidades exactas de operación.
Hoy en día, el sistema de clarificación de cascarilla de molino totalmente automatizado del cliente funciona sin ninguna interacción humana. El agua reciclada utilizada en los procesos de la planta es más limpia y requiere menos tratamiento. El agua más limpia también resulta en menos reparaciones de equipos de la planta. Además, los técnicos pueden completar de manera más eficiente sus principales responsabilidades, dejando que la tecnología de automatización controle el sistema de clarificación. La reubicación del equipo de monitoreo fuera de la grúa ha creado un entorno de trabajo mucho más seguro y, con análisis y diagnósticos continuos, los operadores pueden mantenerse más informados del estado del sistema, lo que ayuda a planificar el mantenimiento del equipo. En conjunto, todas estas mejoras han creado una acería más segura y eficiente para el cliente.
Sistema automatizado de grúa de foso a escala
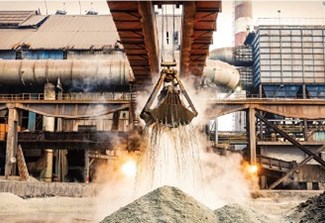