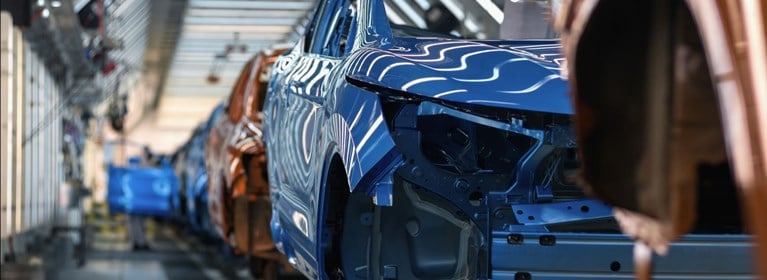
Système automatisé de monorail d’assemblage de bus
Industrie automobile | Technologie d’alimentation et de mouvement | Par Magnétek | 14 nov. 2011
Historique
Un fabricant d’autobus nord-américain voulait automatiser son nouvel assemblage de modèles de véhicules pour augmenter la productivité tout en maintenant des normes de qualité élevées. Afin d’obtenir le débit accru requis, l’entreprise a décidé d’installer deux systèmes de monorail identiques. Chaque système de monorail à 3 porte-avions a été conçu pour déplacer des pièces de véhicule d’un convoyeur d’assemblage vers la carrosserie du véhicule située sur un système de convoyeur au sol.
Description du système
Le mouvement de levage est contrôlé par un entraînement IMPULSE® P3 Série 2, et le mouvement du chariot sur le support est contrôlé par l’entraînement V7 Yaskawa. Le transporteur fonctionne manuellement autour du système de monorail grâce à l’utilisation d’une station de pendentif sbp2 à 10 boutons. La station de pendentif, qui pend sous le transporteur, contrôle tous les mouvements de levage et de transporteur. Un pneu porteur (tracteur) est utilisé pour guider solidement le transporteur autour du monorail. Le mouvement du transporteur n’est pas autorisé tant que le pneu du tracteur n’est pas complètement engagé. Des capteurs photoélectriques sont utilisés pour positionner les porteurs et pour empêcher les transporteurs de se percer.
Fonctionnement du système
Les transporteurs sont en file d’attente au début du système de monorail, en attendant que le processus d’assemblage du moteur au châssis commence. Un opérateur commence le processus en marchant manuellement sur le support vide jusqu’à la position de chargement, qui est située au-dessus du convoyeur d’assemblage du moteur. Une fois que le moteur est chargé sur le palan, l’opérateur déplace manuellement le transporteur sur le système de convoyeur au sol pour décharger le moteur dans la carrosserie du véhicule.
Pendant l’opération d’assemblage, l’opérateur peut lancer une commande de « vitesse de ligne » qui synchronise la vitesse du transporteur pour correspondre à celle du système de convoyeur au sol, et déplace automatiquement le transporteur tout au long du processus d’assemblage. Cette synchronisation est réalisée grâce à l’utilisation de la communication RF entre le transporteur et le système de convoyeur au sol. Une fois que la pièce a été installée dans le corps du véhicule, l’opérateur lance une commande de « retour » pour renvoyer automatiquement le transporteur vide à la zone de file d’attente.
Si une commande de retour n’a pas été émise au moment où le transporteur atteint la fin de la chaîne de montage, le transporteur s’arrêtera et une alarme retentit pour alerter l’opérateur. Une fois que la commande de retour a été émise, le klaxon d’alarme s’arrêtera et le transporteur se déplacera automatiquement de nouveau à la zone de file d’attente.
Si un autre transporteur est situé à l’intérieur des paramètres de distance prédéfinis du transporteur voyageur, le transporteur voyageur ralentira et/ou s’arrêtera pour éviter d’entrer en collision avec le transporteur devant lui.