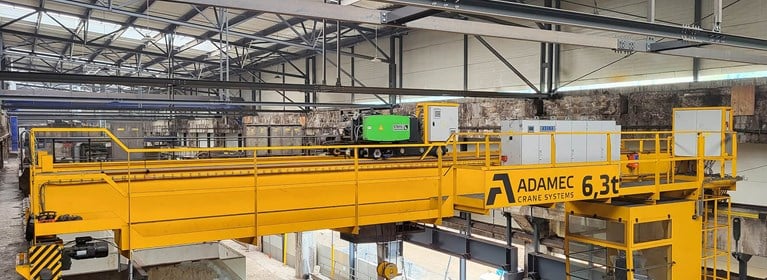
Crane technology for harsh foundry operations
Modernisation of an iron foundry with crane technology from STAHL CraneSystems
Fabrication | Métallurgie | Structures Porteuses | Levage | par CMCO | 18 févr. 2025
As part of a comprehensive refurbishment, the PROMET foundry in Vsetín has invested in new crane systems. The cranes have to be designed for a high dust load, and able to work at temperatures of over 55 °C in some cases. Czech system integrator Adamec, a longstanding STAHL CraneSystems sales partner and crane builder, carefully planned the extensive project and carried out the complex installation during ongoing foundry operations.
The town of Vsetín is situated in the easternmost part of the Czech Republic, close to the border with Slovakia. The countryside and forests of the Moravian-Silesian Beskids are a nature conservation area, and the region is a considered an attractive recreation and holiday destination. More than half of the total area of the Vsetín district is forests. This probably explains why environmental and sustainability concerns are so important to the industrial companies based there.
Reduce environmental impact while increasing efficiency
Almost 40% of the working population in the Vsetín district is employed in industry. The family-run PROMET Group employs over four thousand people in the Czech
Republic and internationally. It comprises more than forty companies operating in the fields of machine construction, metallurgy and engineering. In Vsetín, the Group has an iron foundry that sought to achieve efficiency gains while also improving its environmental footprint.
As major consumers of energy and raw materials, foundries have a particular obligation to protect the environment by limiting emissions, conserving resources and meeting the requirements of applicable standards and laws. The PROMET foundry employs 84 people and has a capacity of 8,000 tonnes of castings per year. It supplies manufacturers of lifts and escalators, electric motors, pumps, textile and knitting machines, as well as the shipbuilding industry.
Products are made of grey cast iron and ductile iron – a type of cast iron in which the graphite in the iron is in the form of nodules, and which has mechanical properties similar to steel (spheroidal graphite cast iron). More than half of the foundry’s total capacity goes to export markets, typically to major European customers. With many years of experience, the PROMET foundry in Vsetín is able to produce everything from small parts weighing several tens of kilograms up to complex cast components weighing several tonnes.
Castings are manufactured on a new manual and an automatic production line. On the automatic production line, the company makes parts weighing around 90 kilograms. On the manual production line, castings weighing between 100 and 5,000 kg are produced in modern medium-frequency induction melting furnaces. The furnaces have a production capacity of 4.3 tonnes of molten iron per hour.
Modernising technology and buildings
The PROMET foundry in Vsetín was renovated and modernised in 2022 and 2023. Its crane systems were also affected by the refurbishment and were extensively renewed. Modernisation was needed to improve the plant’s efficiency and environmental parameters, for example through greening and modifications to the foundry building. With the European Union providing a grant of more than 50% of the total costs, the investments have been worthwhile: solid particulate emissions have since been reduced by 92%.
The modernisation involved the entire foundry building, including complete reconstruction and insulation of the roof and facade. Structural alterations were carried out to accommodate the latest technology and equipment, including a melting furnace, a blasting system, a painting booth, and extraction and filter systems. In addition, state-of-the-art crane technology has been installed throughout the plant to reduce production costs, increase safety, and meet legal standards for all hoists. The new crane systems have been in operation since the beginning of 2023.
Crane technology for automatic and manual casting processes
STAHL CraneSystems supplied all the hoists for this project. Adamec is a longstanding supplier for the Czech market – up to 150 joint projects are realised each year. The STAHL CraneSystems brand stands for reliable and safe hoists and crane components as well as methodical engineering solutions. The portfolio includes slewing jib cranes, single and double girder overhead travelling cranes, suspension cranes, Goliath and semi-portal cranes as well as bracket cranes for a S.W.L. range from 125 kg to 250,000 kg.
Adamec Crane Systems is a Czech company specialising in the design, manufacture and installation of crane systems. It offers made-to-measure solutions especially for heavy-duty applications in various sectors, primarily industry and construction. Adamec Crane Systems focuses on the production of bridge, gantry and floor-mounted jib cranes as well as customisable lifting systems for special applications. The company has developed its own calculation and design software for this purpose.
Complete refit of the crane systems
The PROMET project required the complete refitting of the existing crane systems and a significant expansion of the hoist infrastructure. What made the project special was the size of the order and the number of cranes. Several single and double girder cranes for loads of 5, 6, 10 and 12.5 tonnes were needed – both with an operator platform and with the option for external remote control of the crane. There were also several wall and floor mounted jib cranes with a reach (crane jib length) of 3 m for loads of up to 3,000 kg and 4 m for weights of up to 500 kg.
Double girder and single girder cranes have different designs and are optimised for specific applications and requirements. Single girder cranes are well suited for smaller, medium loads and spaces with limited height. They are economical and ideal for workshops and medium-sized industrial operations. Double girder cranes are designed for heavier loads and larger spaces where a greater span and large lifting heights of up to 10 metres and more are required. They offer a more robust, more stable solution for heavy-duty applications and are generally more cost-intensive.
Extremely high demands on the crane technology
When installing crane systems in an iron foundry, special requirements must be taken into account to ensure the efficiency and safety of the system. Castings often weigh several tonnes. For this reason, the crane system mechanisms should offer fine control for precise lifting and lowering as well as for the horizontal movements of such large loads. The new double girder cranes now travel at speeds of 6 to 60 m/min; the trolley has a horizontal travelling speed of 2.5 to 30 m/min and a well-controlled lifting speed under load of 0.16 to 8 m/min. A high level of shock and vibration damping also assists the stable handling of heavy castings.
The crane technology used in foundries must be designed for a high dust load. The systems should therefore have high-strength, dust-protected (encapsulated) components. Extreme temperatures often occur in foundries. The crane systems must be made of materials that can withstand the high temperatures of over 55 °C in the PROMET foundry and ensure uninterrupted operation. Electrical components should be positioned so that they are not directly exposed to heat.
Quality and reliability with TDC hoists
At the furnaces, ladle cranes are used to transport the molten metal. These are subject to higher safety requirements – also for their electronics and electrics – in Performance Level d. This is why only hoists with redundant Twin Drive Concept (TDC) design are used here, as these are ideally suited for transporting molten metal and materials with a similar hazard potential. For other goods, the load can be as much as 60% higher. The Twin Drive Concept prevents the load from dropping if the gearbox breaks.
TDC wire rope hoists are equipped with two motor-gear units as standard. Both motors are controlled synchronously – as are the brakes, which function as service and safety brakes simultaneously. The brakes are designed so that they can each brake or hold the load alone in an emergency. Permanent load, drive and brake monitoring on TDC hoists is carried out by STAHL CraneSystems condition monitoring systems.
The combination of heat, heavy loads and machinery poses particular safety risks. Because of the harsh operating environment, frequent maintenance is required to ensure the reliability and longevity of the cranes. Adamec offers appropriate maintenance contracts in this regard.
Conclusion
During the refurbishment, the biggest challenge was that production could only be partially shut down, meaning that some of the installation work had to be carried out in night shifts. The customer was very satisfied with the competent advice, careful planning and trouble-free installation under difficult conditions. Now the cranes are coping with the harsh conditions in the foundry without any difficulties or downtime.
Authors
David Adamec is Managing Director of Adamec Crane Systems in Prague.
Heike Metzger is Senior Specialist, Sales Enablement at STAHL CraneSystems
in Künzelsau.
Images and captions
Remote-controlled single girder crane for loads up to 10,000 kg with a span of 12.9 meter
Specially customised ACS-3t/3m floor-mounted jib cranes
ACS-5t/12.9m double girder crane in the foundry process, exposed to dust and high temperatures
As far as possible, the crane systems were to be installed without interrupting operations at the foundry
ACS-6.3t/12.9m double girder crane with operating platform and controls in the cab
It was a big order, including double girder cranes for large loads as well as
ACS-6.3t/12.9m single girder cranes and ACS-3t/3m floor-mounted jib cranes
Conveyor line with lifting technology facilitates the handling of cast parts