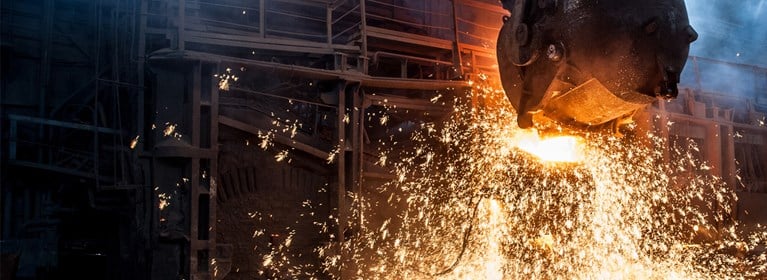
Sistema automatizzato di monorotaia in metallo caldo
Metallurgia | Crane Systems | presso Magnetek | 01 set 2011
Sfondo
È stata costituita un'impresa comune tra un'impresa americana e una messicana per la produzione di acciaio. Il nuovo laminatoio necessitava di un mezzo per spostare l'acciaio fuso tra i forni di fusione e le aree di colata. Si è deciso che il metodo migliore per farlo era quello di installare un anello di monorotaia con tre portaerei. Per aiutare l'operatore nel posizionamento del carico, è stata aggiunta una funzione di invio automatico.
Descrizione del sistema
Il movimento del paranco è controllato da un azionamento IMPULSE® P3 Serie 2 e il movimento del carrello sul supporto è controllato dall'azionamento V7 Yaskawa. Il supporto aziona il meccanismo di inclinazione della benna. Il posizionamento del paranco avviene tramite un finecorsa a quattro posizioni e il posizionamento del carrello avviene tramite sensori di prossimità. Un PLC Allen-Bradley ControlLogix controlla l'operazione di invio automatico. Un sistema radio remoto Magnetek consente a uno qualsiasi dei sei trasmettitori di controllare una qualsiasi delle tre portanti, in base a un metodo "primo arrivato, primo servito". Un ciondolo può essere collegato a uno qualsiasi dei supporti per controllarli nel caso in cui una radio si guasti. I sensori fotoelettrici vengono utilizzati per evitare che i portatori si scontrino l'uno con l'altro.
SFOGLIA I NOSTRI AZIONAMENTI A IMPULSI®
Funzionamento del sistema
Prima che l'acciaio venga versato nella benna, la benna viene rivestita nell'area di trattamento della lega. Dopo essere stato trattato, l'operatore sposta manualmente il supporto e la benna nell'area di fusione utilizzando il trasmettitore radio. Quando il trasportatore raggiunge l'area di fusione, l'operatore abbassa la benna al livello più basso per consentirne lo spostamento sotto ostacoli in prossimità dei forni. Una volta posizionato in una delle quattro posizioni di versamento, il secchio viene riempito manualmente e quindi allontanato manualmente dall'area. Quando si allontana dalla posizione di versamento, l'operatore posiziona la radio in modalità automatica, commuta l'invio sulla posizione di versamento #1 o #2 e spegne il trasmettitore. Il trasmettitore deve essere spento per consentire all'operatore successivo di prendere il controllo della portante con il suo trasmettitore. Il paranco sale quindi in posizione completamente sollevata e inizia a viaggiare verso la posizione di getto selezionata. Il vettore continua verso la posizione di colata, rallentando in curva. Quando il corriere raggiunge la posizione selezionata, si ferma. L'operatore successivo accende quindi il suo trasmettitore e lo mette in manuale per versare l'acciaio fuso. Dopo che l'operatore ha finito di versare, mette il supporto in automatico, preme il pulsante di invio e spegne il trasmettitore. Il paranco si solleva quindi in posizione di massimo sollevamento e procede verso l'area di trattamento della lega. Durante la marcia in curva e quando ci si avvicina all'area di trattamento della lega, il supporto funziona a bassa velocità per fornire un ulteriore livello di sicurezza per la movimentazione con acciaio fuso. Quando il trasportatore raggiunge l'area di trattamento della lega, si ferma e l'operatore successivo prende manualmente il controllo del vettore. Il ciclo si ripete quindi.